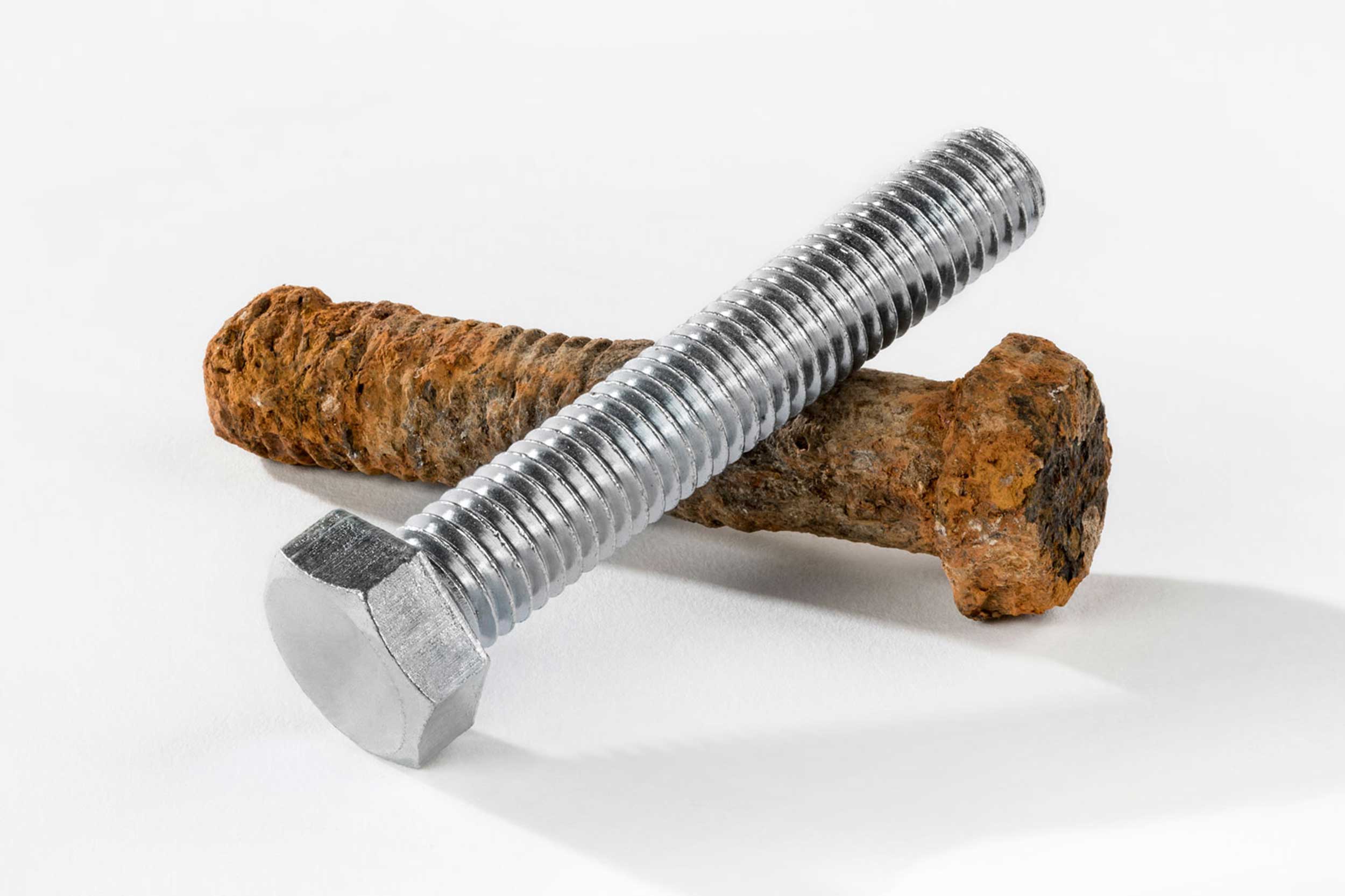
Corrosion is a common and persistent problem that affects various materials, including metals. One specific type of corrosion that has garnered significant attention is alloy corrosion. Alloys, which are a combination of two or more metals, are widely used in industries ranging from construction to manufacturing. They offer enhanced properties like strength, durability, and resistance to wear and tear. However, even alloys are not immune to the damaging effects of corrosion.
In this article, we will delve into the fascinating world of alloy corrosion and explore 18 extraordinary facts that every chemistry enthusiast and industry professional should know. From the different types of alloy corrosion to the mechanisms behind this process and the ways to prevent it, we will uncover the intricate details of this phenomenon. So, fasten your seatbelts and get ready for an informative and engaging journey into the captivating realm of alloy corrosion!
Key Takeaways:
- Alloy corrosion is a natural process where metals like iron and aluminum deteriorate over time. It can be prevented by using protective coatings and proper maintenance.
- Saltwater and high temperatures can speed up alloy corrosion, affecting buildings, infrastructure, and even electronic devices. Scientists are working on innovative solutions to combat this issue.
Corrosion is a natural process that occurs when metals react with their environment.
Alloy corrosion is a common phenomenon that affects various types of metals. It is a natural process where metals, such as iron, aluminum, or copper, react with their surrounding environment, resulting in the deterioration of the material over time.
The primary cause of alloy corrosion is electrochemical reactions.
When an alloy comes into contact with moisture or corrosive substances, it creates an electrochemical cell. This cell allows the transfer of electrons, leading to the oxidation of the metal, commonly known as corrosion.
Saltwater is highly corrosive to most alloys.
One of the most significant factors that accelerate corrosion is exposure to saltwater. The high concentration of salt in seawater acts as an electrolyte, intensifying the electrochemical reactions and speeding up the corrosion process.
Some alloys are more resistant to corrosion than others.
Not all alloys are created equal when it comes to corrosion resistance. Certain alloys, such as stainless steel or titanium, have inherent properties that make them highly resistant to corrosion, making them ideal for applications in harsh environments.
Galvanic corrosion occurs when two dissimilar metals come into contact.
When two dissimilar metals are in contact with each other, along with an electrolyte like water, a galvanic cell is formed. The more active metal becomes the anode, while the less active metal becomes the cathode, leading to accelerated corrosion of the anode.
Alloy corrosion can be prevented or minimized through various methods.
To protect alloys from corrosion, several techniques can be employed. These include applying protective coatings, using sacrificial anodes, implementing cathodic protection, and controlling the environment through proper maintenance and storage.
Crevice corrosion is a specific type of localized corrosion that occurs in narrow crevices.
In crevice corrosion, small gaps or crevices in an alloy structure can trap corrosive substances, leading to accelerated corrosion within those confined spaces. This type of corrosion can be particularly damaging and difficult to detect.
High temperatures can increase the rate of alloy corrosion.
Elevated temperatures can enhance the chemical reactions involved in corrosion, leading to faster degradation of alloys. This is especially important to consider in industrial settings where high temperatures are common.
Alloy corrosion can compromise the structural integrity of buildings and infrastructure.
When alloys used in the construction of buildings, bridges, or other infrastructure are corroded, their strength and load-bearing capabilities can be significantly weakened. It is essential to regularly inspect and maintain such structures to prevent potential disasters.
Alloy corrosion can be influenced by the pH level of the surrounding environment.
The acidity or alkalinity of the environment in which alloys are exposed can impact the rate of corrosion. Acidic environments tend to accelerate corrosion, while alkaline environments may slow it down.
Alloy corrosion can be a major concern in the automotive industry.
Automobiles are exposed to various environmental conditions, including moisture, road salt, and pollutants, making them susceptible to corrosion. Manufacturers employ corrosion-resistant alloys and protective coatings to mitigate its impact on vehicle longevity.
The use of inhibitors can mitigate alloy corrosion.
Corrosion inhibitors are substances that can be added to an environment to slow down or prevent corrosion. They work by creating a protective barrier on the alloy’s surface, reducing its interaction with corrosive agents.
Alloy corrosion can lead to financial losses and increased maintenance costs.
Corrosion damage can be costly to repair or replace. Industries and infrastructure sectors invest significant resources into combating corrosion to minimize financial losses and ensure the longevity of their assets.
Proper alloy selection can significantly reduce the risk of corrosion.
Choosing the right alloy for specific applications can greatly contribute to corrosion resistance. Factors such as exposure conditions, environment, and intended use should be considered during the alloy selection process.
Alloy corrosion can impact the performance and lifespan of electronic devices.
Electronic devices with exposed metal components, such as smartphones or computers, are vulnerable to corrosion. The degradation of these metal parts can affect the functionality and overall lifespan of the devices.
Alloy corrosion can be influenced by the presence of impurities in the metal.
Impurities present in the alloy’s composition can exacerbate the corrosion process. Small amounts of certain elements or compounds can promote localized corrosion, making the alloy more susceptible to degradation.
Environmental factors, such as humidity and temperature, can affect the rate of alloy corrosion.
Different environmental conditions can accelerate or decelerate the corrosion rate of alloys. Higher humidity levels and elevated temperatures generally increase corrosion rates, while drier environments and lower temperatures can slow it down.
Alloy corrosion research and development aim to find innovative solutions.
Scientists and engineers continuously work on developing new materials and techniques to combat alloy corrosion. Ongoing research focuses on improving alloy compositions, surface treatments, and corrosion prevention methods to reduce the impact of corrosion in various industries.
Conclusion
In conclusion, alloy corrosion is a complex phenomenon that can have both detrimental and beneficial effects. Understanding the factors that contribute to corrosion can help in the development of corrosion-resistant alloys and the prevention of costly damage to structures and equipment. By selecting the appropriate alloy composition, implementing protective coatings, and employing corrosion mitigation techniques, we can extend the lifespan and durability of metal components.Furthermore, with ongoing research and advancements in the field of corrosion science, new solutions and treatments are being developed to combat the challenges posed by alloy corrosion. By staying informed about the latest developments and implementing proactive measures, we can effectively address the issues related to alloy corrosion and ensure the longevity of various metal-based applications.
FAQs
Q: What causes alloy corrosion?
A: Alloy corrosion is caused by several factors, including exposure to moisture, chemicals, and changes in temperature. It can also be accelerated by galvanic corrosion, where two dissimilar metals come into contact in the presence of an electrolyte.
Q: How can alloy corrosion be prevented?
A: Alloy corrosion can be prevented through various methods, including the application of protective coatings, such as paints or corrosion inhibitors. Regular maintenance, including cleaning and inspection, can also help identify and address potential corrosion issues.
Q: Can alloy corrosion be reversed?
A: In some cases, if detected early, alloy corrosion can be reversed through treatments like passivation or anodizing. However, it is generally more effective to prevent corrosion from occurring in the first place, rather than trying to reverse it.
Q: Is alloy corrosion a significant problem?
A: Yes, alloy corrosion is a significant problem, costing industries billions of dollars each year in repairs, replacements, and maintenance. It affects a wide range of sectors, including manufacturing, infrastructure, and transportation.
Q: Are there any benefits to alloy corrosion?
A: Yes, in some cases, corrosion can result in the formation of protective layers, such as patina on bronze or rust on iron, which can help protect the underlying alloy from further corrosion. Additionally, corrosion studies have led to the development of more resistant alloys and innovative coatings.
Was this page helpful?
Our commitment to delivering trustworthy and engaging content is at the heart of what we do. Each fact on our site is contributed by real users like you, bringing a wealth of diverse insights and information. To ensure the highest standards of accuracy and reliability, our dedicated editors meticulously review each submission. This process guarantees that the facts we share are not only fascinating but also credible. Trust in our commitment to quality and authenticity as you explore and learn with us.