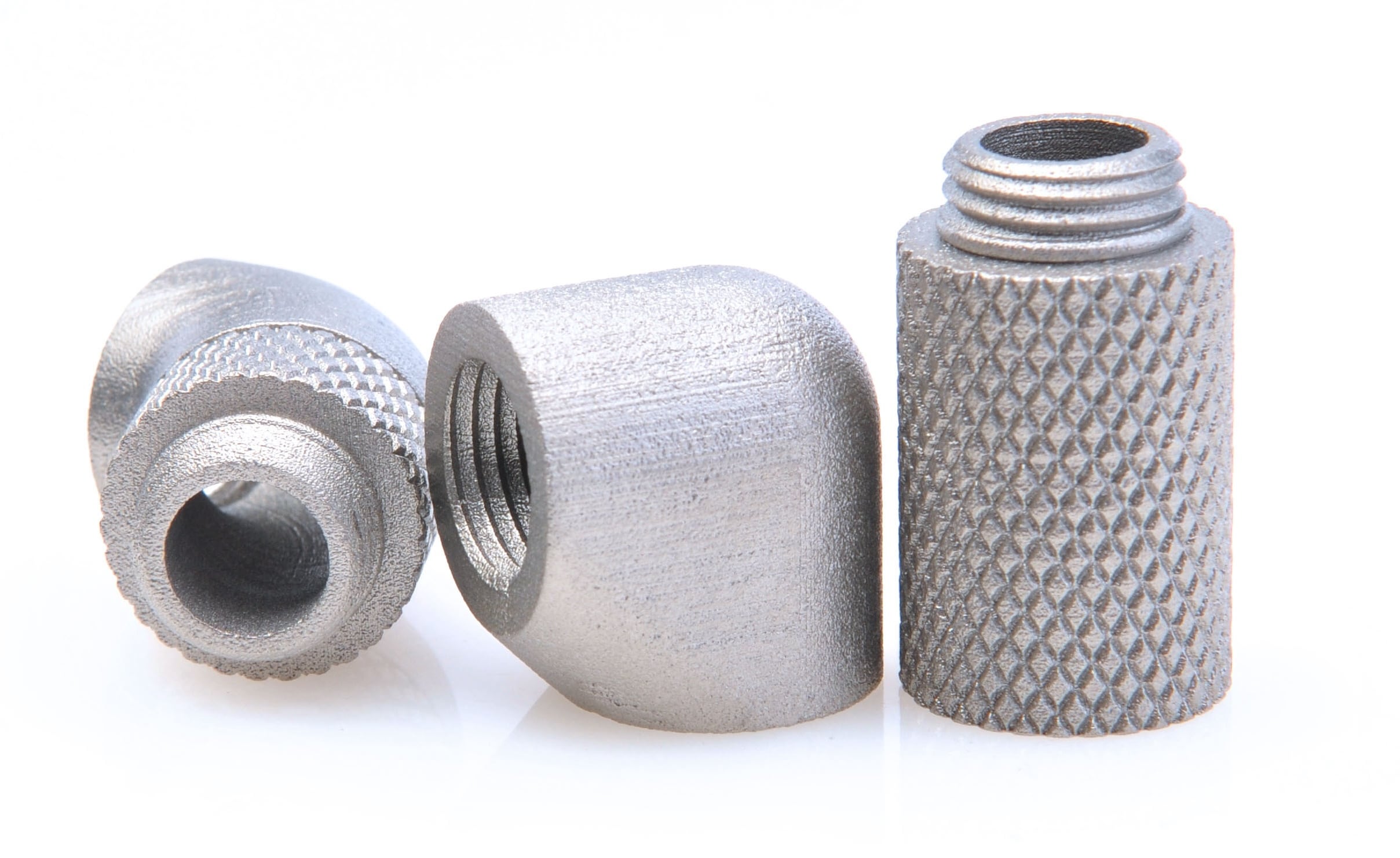
Inconel is a superalloy known for its exceptional strength and resistance to extreme temperatures. But what makes this material so special? Inconel alloys are primarily composed of nickel and chromium, which give them their remarkable properties. These alloys are used in some of the most demanding environments, from jet engines to deep-sea exploration. Inconel can withstand temperatures that would melt most other metals, making it invaluable in aerospace and power generation industries. Curious about the specifics? Here are 40 facts that will give you a deeper understanding of this incredible material. Buckle up, because Inconel is about to blow your mind!
Key Takeaways:
- Inconel is a superalloy known for resisting high temperatures and corrosion, making it ideal for aerospace, medical, and energy applications. Its future looks bright with ongoing research and development for new and advanced uses.
- Inconel's unique composition and properties, along with its recyclability and energy efficiency, make it a valuable material despite its challenges. Ongoing efforts in research and development are driving the demand for this versatile alloy.
What is Inconel?
Inconel is a family of nickel-chromium-based superalloys known for their exceptional resistance to oxidation and corrosion. These alloys are widely used in extreme environments where high temperatures and pressure are common. Let's dive into some fascinating facts about Inconel.
Composition and Properties
Understanding the composition and properties of Inconel helps us appreciate why it is so special.
- Nickel Content: Inconel alloys typically contain over 50% nickel, which contributes to their high corrosion resistance.
- Chromium Addition: The addition of chromium enhances the alloy's ability to withstand oxidation and high temperatures.
- Molybdenum and Niobium: These elements are often added to improve strength and resistance to pitting.
- High Melting Point: Inconel can withstand temperatures up to 2,600°F (1,427°C), making it ideal for high-heat applications.
- Oxidation Resistance: The alloy forms a stable oxide layer that protects it from further oxidation.
- Non-Magnetic: Inconel is non-magnetic, which is beneficial in applications requiring non-magnetic materials.
- High Strength: Even at elevated temperatures, Inconel maintains its strength and structural integrity.
- Fatigue Resistance: The alloy exhibits excellent fatigue resistance, making it suitable for cyclic loading applications.
Applications of Inconel
Inconel's unique properties make it suitable for a wide range of applications across various industries.
- Aerospace: Used in jet engines, turbine blades, and exhaust systems due to its high-temperature resistance.
- Chemical Processing: Ideal for handling corrosive chemicals and high-temperature reactions.
- Marine Engineering: Used in submarine components and offshore oil rigs for its corrosion resistance.
- Nuclear Reactors: Inconel is used in reactor cores and other components exposed to high radiation and heat.
- Automotive: Employed in turbocharger rotors and exhaust systems to withstand high temperatures.
- Oil and Gas: Used in downhole tools and equipment exposed to harsh environments.
- Power Generation: Inconel is used in gas turbines and steam generators.
- Medical Devices: Utilized in surgical instruments and implants due to its biocompatibility.
Manufacturing and Processing
The manufacturing and processing of Inconel involve specialized techniques to maintain its properties.
- Casting: Inconel can be cast into complex shapes, making it versatile for various applications.
- Forging: Forging improves the alloy's mechanical properties and grain structure.
- Machining: Requires specialized tools and techniques due to its hardness and toughness.
- Welding: Inconel can be welded using methods like TIG and MIG, but preheating and post-weld heat treatment are often necessary.
- Heat Treatment: Heat treatment processes like annealing and aging enhance the alloy's properties.
- Cold Working: Cold working increases the strength and hardness of Inconel.
- Surface Treatments: Coatings and surface treatments can further enhance corrosion resistance.
Historical Background
The history of Inconel is as fascinating as its properties.
- Development: Inconel was developed by the International Nickel Company (INCO) in the 1940s.
- First Uses: Initially used in the aerospace industry for turbine blades and other high-temperature components.
- Evolution: Over the years, various grades of Inconel have been developed to meet specific industry needs.
- Patents: Numerous patents have been filed for different compositions and processing methods of Inconel.
Environmental Impact
Inconel's environmental impact is an important consideration in its use.
- Recyclability: Inconel is highly recyclable, reducing its environmental footprint.
- Energy Efficiency: Its high-temperature resistance contributes to energy efficiency in industrial processes.
- Longevity: The durability of Inconel reduces the need for frequent replacements, minimizing waste.
- Corrosion Resistance: Reduces the release of harmful substances into the environment.
Challenges and Limitations
Despite its many advantages, Inconel has some challenges and limitations.
- Cost: Inconel is more expensive than many other materials, which can be a limiting factor.
- Machinability: Its hardness and toughness make it difficult to machine, requiring specialized equipment.
- Availability: Not as widely available as more common materials, which can lead to supply chain issues.
- Weight: Inconel is relatively heavy, which can be a drawback in weight-sensitive applications.
Future of Inconel
The future of Inconel looks promising with ongoing research and development.
- New Alloys: Researchers are developing new Inconel alloys with enhanced properties.
- Additive Manufacturing: 3D printing techniques are being explored for producing complex Inconel components.
- Sustainability: Efforts are being made to improve the sustainability of Inconel production and recycling.
- Advanced Applications: Emerging technologies in aerospace, medical, and energy sectors are driving demand for Inconel.
- Global Demand: As industries continue to push the boundaries of performance, the demand for Inconel is expected to grow.
The Final Word on Inconel
Inconel, a superalloy, stands out for its remarkable strength and resistance to extreme conditions. Used in aerospace, nuclear reactors, and chemical processing, this material handles high temperatures and corrosive environments with ease. Its nickel-chromium composition provides oxidation resistance, making it ideal for turbine blades and exhaust systems.
Despite its high cost, the benefits of Inconel often outweigh the expense. Its durability and longevity reduce the need for frequent replacements, saving money in the long run. Engineers and scientists continue to explore new applications, pushing the boundaries of what this superalloy can achieve.
Understanding Inconel's properties and uses helps appreciate its importance in modern technology. Whether in space exploration or industrial manufacturing, Inconel remains a key player in advancing innovation and efficiency.
Frequently Asked Questions
Was this page helpful?
Our commitment to delivering trustworthy and engaging content is at the heart of what we do. Each fact on our site is contributed by real users like you, bringing a wealth of diverse insights and information. To ensure the highest standards of accuracy and reliability, our dedicated editors meticulously review each submission. This process guarantees that the facts we share are not only fascinating but also credible. Trust in our commitment to quality and authenticity as you explore and learn with us.