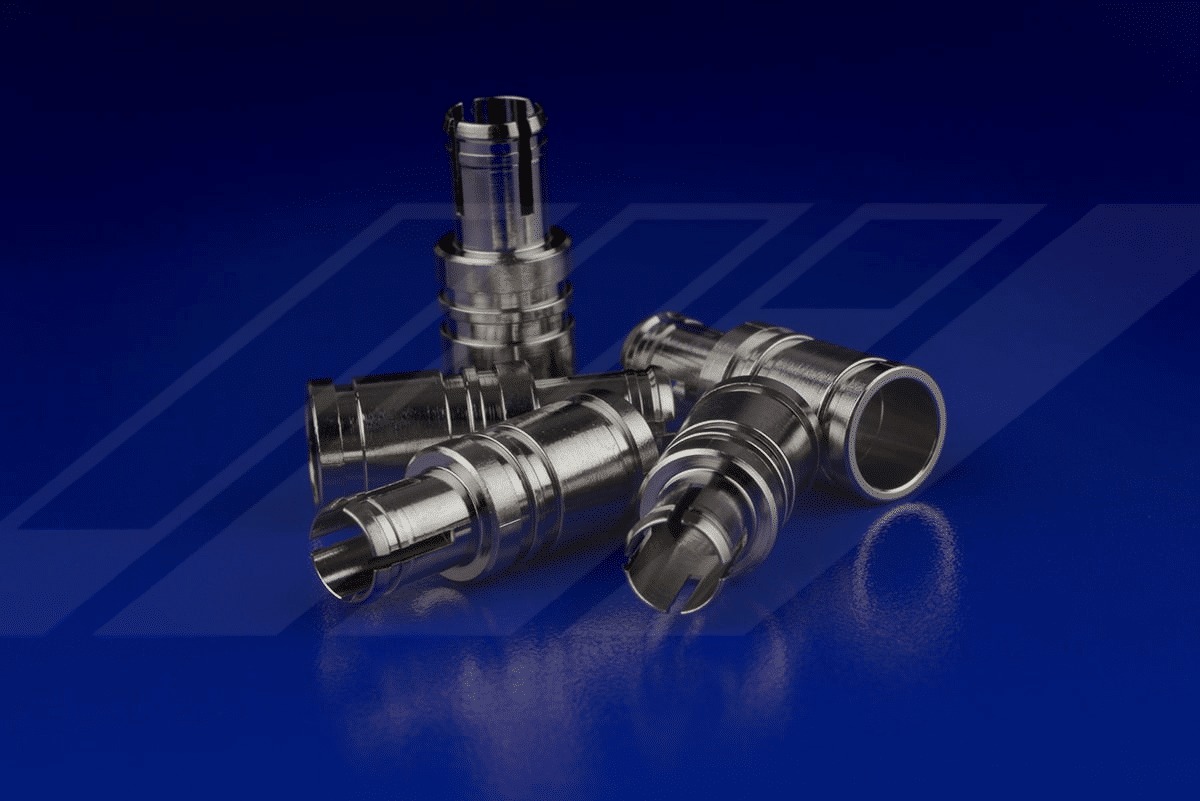
Electroless plating is a method of depositing a metal coating on a surface without using an electric current. This technique offers several advantages, such as uniform thickness and the ability to coat complex shapes. Electroless plating is widely used in industries like electronics, automotive, and aerospace due to its reliability and efficiency. But what makes this process so special? Here are 14 fascinating facts about electroless plating that will help you understand its importance and applications. From its history to its modern-day uses, these facts will give you a comprehensive overview of this remarkable technology.
What is Electroless Plating?
Electroless plating is a method of depositing a metal coating on a substrate without using an electric current. This technique offers several advantages over traditional electroplating, making it a popular choice in various industries.
-
Chemical Reaction: Electroless plating relies on a chemical reduction reaction to deposit the metal. This process doesn't need an external power source, unlike electroplating.
-
Uniform Coating: One of the biggest advantages is the uniformity of the coating. Electroless plating ensures an even layer of metal, even on complex shapes and surfaces.
-
Corrosion Resistance: The coatings produced by electroless plating are highly resistant to corrosion. This makes it ideal for applications in harsh environments.
Applications of Electroless Plating
Electroless plating is used in a wide range of industries due to its versatility and effectiveness. Here are some key applications:
-
Electronics: In the electronics industry, electroless plating is used to create conductive surfaces on non-conductive materials. This is crucial for manufacturing printed circuit boards (PCBs).
-
Automotive: The automotive sector uses electroless plating for parts that require high wear resistance and durability, such as fuel injectors and brake components.
-
Aerospace: Aerospace components often undergo electroless plating to enhance their resistance to wear and corrosion, ensuring they can withstand extreme conditions.
Types of Electroless Plating
There are different types of electroless plating, each with unique properties and applications. Understanding these types can help in selecting the right one for a specific need.
-
Nickel Plating: Electroless nickel plating is the most common type. It provides excellent corrosion resistance and hardness, making it suitable for various industrial applications.
-
Copper Plating: Electroless copper plating is often used in the electronics industry for creating conductive layers on non-metallic surfaces.
-
Gold Plating: This type is used for applications requiring high conductivity and resistance to oxidation, such as in connectors and switches.
Advantages of Electroless Plating
Electroless plating offers several benefits that make it a preferred choice in many applications. Here are some of the key advantages:
-
No Need for Electricity: Since it doesn't require an electric current, electroless plating can be used on non-conductive materials, expanding its range of applications.
-
Cost-Effective: The process can be more cost-effective than traditional electroplating, especially for complex shapes that require uniform coatings.
-
Improved Adhesion: The coatings produced by electroless plating often have better adhesion to the substrate, resulting in a more durable finish.
Challenges in Electroless Plating
Despite its many advantages, electroless plating also comes with some challenges. Understanding these can help in optimizing the process and achieving better results.
-
Chemical Management: The chemicals used in electroless plating need to be carefully managed to ensure consistent results and avoid contamination.
-
Waste Disposal: Proper disposal of the chemicals and waste generated during the process is crucial to minimize environmental impact.
Electroless Plating's Impact
Electroless plating has revolutionized various industries with its unique advantages. Unlike traditional methods, it doesn't require electricity, making it more versatile and cost-effective. This process ensures uniform coating, even on complex shapes, enhancing durability and resistance to corrosion. Industries like electronics, automotive, and aerospace benefit significantly from this technology. Its ability to deposit metals like nickel, copper, and gold opens up endless possibilities for innovation. As technology advances, electroless plating continues to evolve, offering even more efficient and environmentally friendly solutions. Understanding these facts highlights the importance of electroless plating in modern manufacturing and its potential for future applications. Whether you're a student, engineer, or curious mind, knowing about this process can spark new ideas and appreciation for the science behind everyday objects. Keep exploring and stay curious about the fascinating world of materials science!
Was this page helpful?
Our commitment to delivering trustworthy and engaging content is at the heart of what we do. Each fact on our site is contributed by real users like you, bringing a wealth of diverse insights and information. To ensure the highest standards of accuracy and reliability, our dedicated editors meticulously review each submission. This process guarantees that the facts we share are not only fascinating but also credible. Trust in our commitment to quality and authenticity as you explore and learn with us.