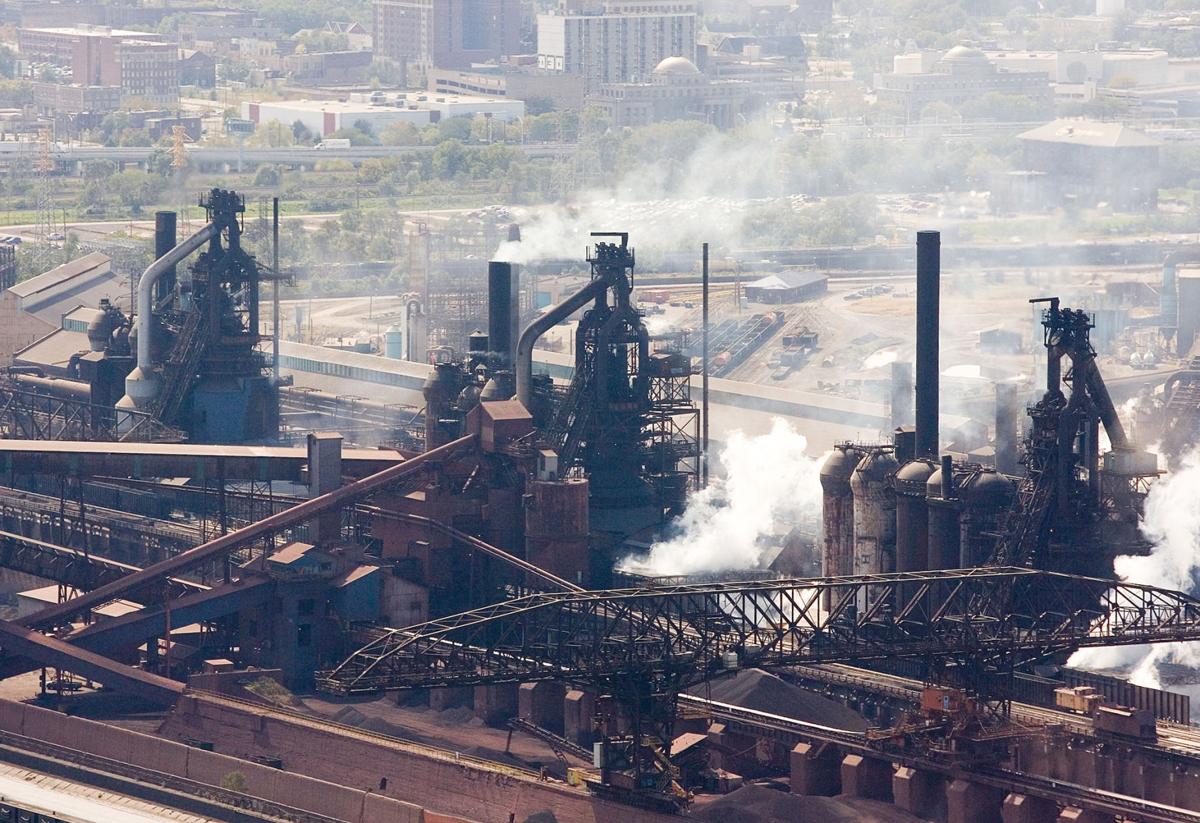
Are you ready to dive into the fascinating world of blast furnaces? In this article, we will explore 13 mind-blowing facts that will take your understanding of these industrial giants to the next level. Blast furnaces are the heart of the iron and steel industry, responsible for producing the raw materials that shape our modern world. While they may appear as colossal structures, there is much more to blast furnaces than meets the eye. From the incredible temperatures and chemistry at play to the historical significance they hold, prepare to be amazed by the secrets hidden within these towering structures. So, fasten your seatbelts and get ready for an informative and thrilling journey into the realm of blast furnaces!
Key Takeaways:
- Blast furnaces are massive structures that operate at extreme temperatures, producing thousands of tons of iron and steel per day. They have been crucial in driving economic growth and continue to evolve with advancements in technology.
- The incredible engineering behind blast furnaces includes precise control of temperature, gas flow, and composition, as well as the capture and use of byproduct gases. Their efficiency and versatility make them vital to the iron and steel industry’s future.
Blast furnaces are massive!
One of the most striking things about blast furnaces is their sheer size. These towering giants can reach heights of up to 100 feet and have a diameter of around 30 feet. This colossal structure is necessary to accommodate the intense heat and necessary materials for the iron-making process.
They operate at extreme temperatures.
Inside the blast furnace, temperatures can soar to a scorching 2,800 degrees Fahrenheit (1,538 degrees Celsius). This extreme heat is required to melt the iron ore and facilitate the chemical reactions necessary for the production of iron and steel.
Blast furnaces are made up of multiple layers.
A typical blast furnace consists of several distinct layers. At the top, there is the charging zone where raw materials such as iron ore, coke, and limestone are introduced. Below that lies the reduction zone, where the iron ore is converted into molten iron. Further down, we find the hearth, where the molten iron collects and is periodically tapped.
They rely on a continuous blast of hot air.
Hot air is blown into the blast furnace through nozzles known as tuyeres. This air, often preheated to maximize efficiency, serves to provide the oxygen necessary for the combustion of coke and the chemical reactions that take place inside the furnace.
Blast furnaces utilize a counter-current flow.
An essential aspect of blast furnace operation is the counter-current flow of materials and gases. As the raw materials descend through the furnace, they encounter gases ascending from the hearth. This flow maximizes the efficiency of heat transfer and chemical reactions.
The byproduct gases are captured for further use.
As the blast furnace operates, various gases are produced as byproducts. These include carbon monoxide, carbon dioxide, and nitrogen. Instead of releasing these gases into the atmosphere, they are captured and used in other industrial processes, such as the generation of electricity or the production of chemicals.
Blast furnaces have a high production capacity.
A single blast furnace is capable of producing thousands of tons of iron and steel per day. This impressive production capacity makes blast furnaces crucial in meeting the global demand for these essential materials.
They have been in use for centuries.
The concept of the blast furnace dates back to ancient China, where the first prototypes were used as early as the 2nd century BC. Over time, blast furnaces evolved and spread to other parts of the world, becoming the backbone of the iron and steel industry.
Blast furnaces require precise control.
The operation of a blast furnace demands careful control of various parameters. Factors like temperature, gas flow, and composition must be closely monitored to ensure optimal efficiency and quality of the iron and steel produced.
They are incredibly efficient.
Despite their massive size and high energy requirements, blast furnaces are remarkably efficient in converting raw materials into iron and steel. Continuous improvements in technology have enabled blast furnaces to achieve high levels of productivity while minimizing waste and energy consumption.
Blast furnace slag has useful applications.
Slag, a byproduct of the iron-making process, has versatile applications. It can be used as a raw material in cement production, road construction, and even as an aggregate in asphalt mixes. This reduces waste and turns it into a valuable resource.
Blast furnaces support economic growth.
The iron and steel industry, heavily reliant on blast furnaces, plays a significant role in driving economic growth. It provides employment opportunities, stimulates local businesses, and contributes to infrastructure development.
Blast furnaces are evolving.
The iron and steel industry is continuously evolving, with advancements in blast furnace technology being a key focus. Innovations aim to increase efficiency, reduce emissions, and enhance sustainability, ensuring blast furnaces remain a vital part of the industry’s future.
So, there you have it – the 13 mind-blowing facts about blast furnaces that showcase the incredible engineering and science behind their operation. These colossal structures have shaped the iron and steel industry for centuries, and with ongoing advancements, they continue to play a crucial role in meeting global demand. The next time you see a blast furnace, you’ll have a deeper appreciation for the complexity and efficiency that lies within.
Conclusion
In conclusion, blast furnaces are truly fascinating structures that play a crucial role in the production of iron and steel. These immense structures are capable of producing large quantities of metal, all while withstanding incredibly high temperatures and intense chemical reactions. From their historical significance to their innovative design, blast furnaces continue to be an integral part of the manufacturing industry.
Whether you’re a chemistry enthusiast or simply interested in the intricacies of industrial processes, learning about blast furnaces can expand your knowledge and appreciation for the world of metallurgy. From the immense heat generated to the complex reactions taking place, blast furnaces are a testament to human ingenuity and the wonders of chemistry.
So the next time you see a blast furnace or hear about its incredible capabilities, remember these mind-blowing facts and marvel at the incredible science behind this engineering marvel.
FAQs
Q: What is a blast furnace?
A: A blast furnace is a massive structure used in the production of iron and steel, where raw materials such as iron ore, coke, and limestone are heated at high temperatures to extract the iron and create molten metal.
Q: How does a blast furnace work?
A: A blast furnace works through a process known as smelting, where the raw materials are loaded into its top and gradually descend towards the bottom, as intense heat is applied from the bottom. This heat causes chemical reactions that result in the extraction of molten iron.
Q: What are some of the key components of a blast furnace?
A: Some key components of a blast furnace include the stack, hearth, bosh, tuyeres, and the charging system. Each component plays a crucial role in ensuring the efficient operation of the furnace and the extraction of iron.
Q: How hot does a blast furnace get?
A: Blast furnaces can reach temperatures as high as 2,700 degrees Fahrenheit (1,500 degrees Celsius) in order to facilitate the chemical reactions necessary for the extraction of molten iron.
Q: Are blast furnaces still used today?
A: Yes, blast furnaces are still used today in the production of iron and steel. Though newer technologies have emerged, blast furnaces continue to be a vital and efficient method for large-scale metal extraction.
Blast furnaces are truly remarkable, but there's so much more to explore in the world of industrial processes and materials science. Delve into the fascinating field of metallurgy, where ancient techniques meet modern innovation. Discover how industrial engineers design and optimize complex systems that drive our world forward. And don't miss the chance to learn about the groundbreaking Bessemer process, which revolutionized steel production and paved the way for the modern age. Each of these topics offers a unique glimpse into the marvels of human ingenuity and the incredible advancements that shape our lives.
Was this page helpful?
Our commitment to delivering trustworthy and engaging content is at the heart of what we do. Each fact on our site is contributed by real users like you, bringing a wealth of diverse insights and information. To ensure the highest standards of accuracy and reliability, our dedicated editors meticulously review each submission. This process guarantees that the facts we share are not only fascinating but also credible. Trust in our commitment to quality and authenticity as you explore and learn with us.