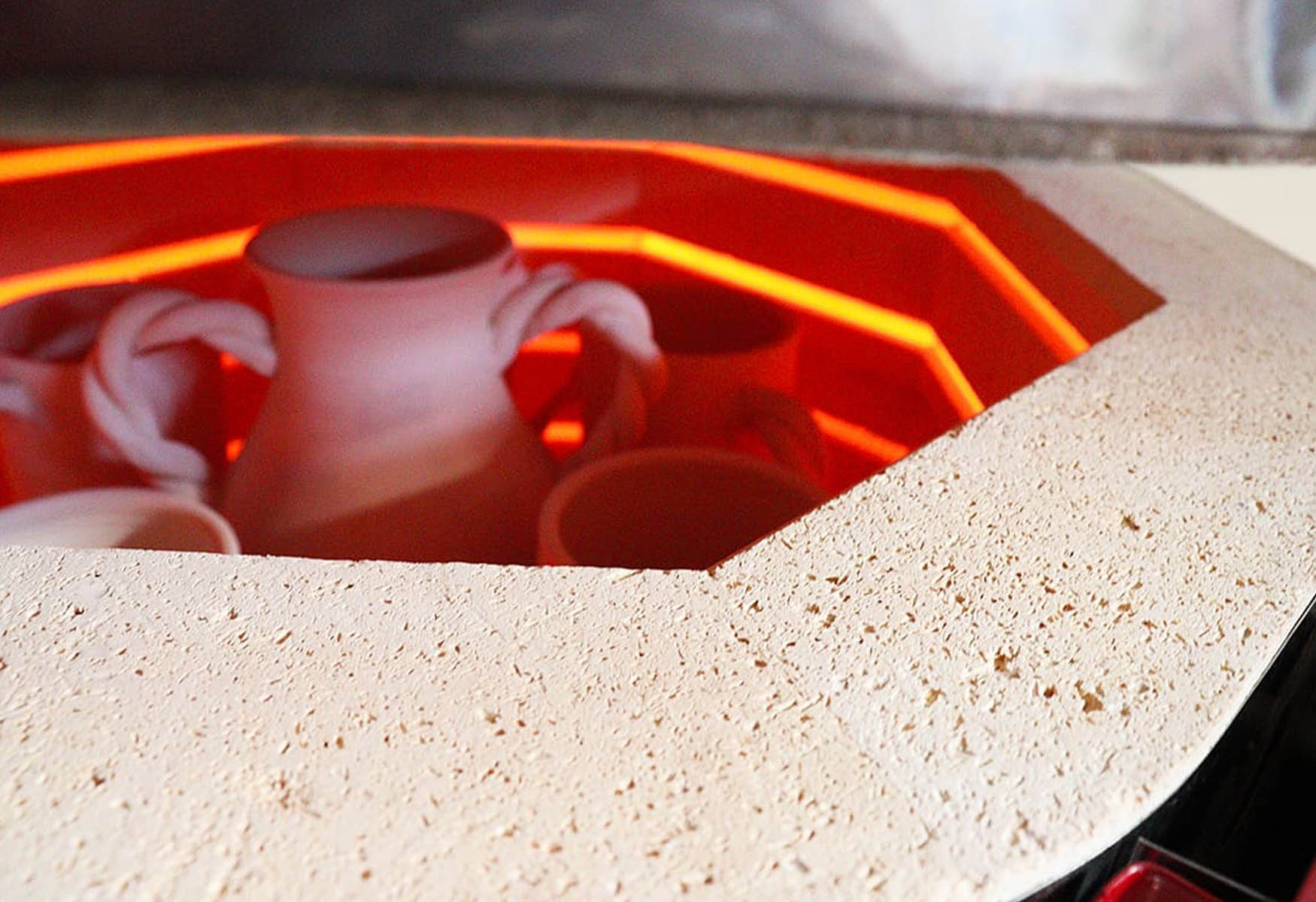
Kiln firing is a fascinating process that has been used for centuries in the creation of ceramic and pottery pieces. It involves heating the objects in a kiln, a specialized oven, to high temperatures to transform clay into durable and beautiful works of art. But did you know that there’s more to kiln firing than meets the eye?
In this article, we will delve into the world of kiln firing and explore some mind-blowing facts that will leave you in awe. From the ancient origins of kiln firing to its modern applications, we will uncover intriguing tidbits about this transformative process. Whether you are a pottery enthusiast, an artist, or simply curious about the world of ceramics, these facts will surely captivate your imagination and deepen your appreciation for the art of kiln firing.
Key Takeaways:
- Kiln firing is an ancient technique used to transform clay into durable ceramic objects. It requires precise temperature control and can create varied surface effects, making it essential for ceramics production.
- Kiln firing is a transformative process that allows artists to create unique effects and bring their creative vision to life. It involves different temperature stages and skilled craftsmanship, turning humble clay into works of art.
Kiln firing is an ancient technique.
Kiln firing has been used for centuries as a method of baking clay and transforming it into durable ceramic objects. The process dates back to ancient civilizations, including the Egyptians and the Chinese.
Kiln firing requires precise temperature control.
The temperature in a kiln must be carefully monitored and controlled throughout the firing process. Different types of clay and glazes require specific temperature ranges to achieve the desired results.
Kiln firing can create varied surface effects.
Depending on the type of firing technique used, kiln firing can result in a wide range of surface effects, including smooth and glossy finishes, textured surfaces, and even dramatic color changes.
Kiln firing allows for the exploration of different firing methods.
There are several firing methods that can be used in a kiln, such as oxidation, reduction, and raku firing. Each method produces distinct results and contributes to the uniqueness of the finished pieces.
Kiln firing is essential for glaze development.
The heat from the kiln melts the glazes applied to the ceramics, creating a glassy surface and sealing the clay body. This process not only enhances the aesthetic appeal but also adds functionality and durability to the finished pieces.
Kiln firing plays a vital role in ceramics production.
From small pottery studios to large-scale industrial ceramic production, kiln firing is a fundamental step in the creation of ceramic artworks, functional pottery, and decorative objects.
Kiln firing can take hours or even days.
Depending on the size of the kiln, the type of clay and glazes used, as well as the desired outcome, firing can sometimes take several hours or even days to complete. Patience and careful monitoring are necessary during this process.
Kiln firing involves different temperature stages.
The firing process typically consists of several temperature stages, including the bisque firing, where the clay is heated to remove any remaining moisture, and the glaze firing, where the glazes are melted and fused to the clay body.
Kiln firing requires skilled craftsmanship.
Mastering the art of kiln firing requires knowledge and skill in understanding temperature control, firing techniques, and the behavior of different clays and glazes. It is a combination of science and art.
Kiln firing can be used to create unique effects.
Artists and potters often experiment with kiln firing to create one-of-a-kind effects such as crystalline glazes, metallic finishes, and smoky, atmospheric effects that add depth and visual interest to their work.
Kiln firing is a transformative process.
From raw clay to finished ceramic pieces, kiln firing is a transformative process that allows artists and craftsmen to bring their creative vision to life. It is the magic that turns humble clay into works of art.
Conclusion
In conclusion, kiln firing is a fascinating process that has been used for centuries to transform raw materials into beautiful and functional objects. From pottery and ceramics to glass and metal, kiln firing plays a crucial role in producing durable and aesthetically pleasing art and everyday items.
Throughout this article, we have explored various mind-blowing facts about kiln firing. We have learned about the different types of kilns, the temperatures they can reach, and the various firing techniques used in different industries. We have also discovered how kiln firing affects the final outcome of the fired objects, including color, texture, and strength.
Whether you are an artist, a collector, or simply someone interested in the world of kiln firing, these facts shed light on the incredible science and artistry behind this process. So the next time you admire a beautifully glazed ceramic bowl or a stunning piece of stained glass, you can appreciate the skill and precision that went into kiln firing it.
FAQs
1. What is kiln firing?
Kiln firing is the process of subjecting objects made of pottery, ceramics, glass, metals, or other materials to high temperatures in a kiln. This heat-based treatment transforms the raw materials into a finished product, making it more durable, decorative, or functional.
2. What types of kilns are used for firing?
Kilns come in various types, including electric kilns, gas-fired kilns, wood-fired kilns, and even solar kilns. Each type has its own unique advantages and is used based on the specific requirements and preferences of the artist or industry.
3. What temperatures can kilns reach during firing?
Kilns can reach extremely high temperatures, ranging from around 1000 degrees Fahrenheit (538 degrees Celsius) for pottery firing to over 2000 degrees Fahrenheit (1093 degrees Celsius) for glass or metal firing, depending on the specific materials being fired and the desired outcome.
4. What are some common firing techniques used in kiln firing?
Some common firing techniques include oxidation firing, reduction firing, salt firing, and raku firing. Each technique involves specific conditions and atmospheres within the kiln to achieve different effects on the finished product.
5. How does kiln firing affect the final outcome of the fired objects?
Kiln firing plays a significant role in determining the color, texture, strength, and even the shape of the final fired objects. Factors such as the temperature, firing time, choice of glazes or finishes, and the kiln atmosphere all contribute to the unique characteristics of the finished piece.
6. Can any material be fired in a kiln?
No, not all materials are suitable for kiln firing. Materials that can withstand high temperatures without melting or breaking down can be safely fired in a kiln. Examples include clay, porcelain, glass, and certain types of metals.
Kiln firing is a fascinating process that transforms raw clay into beautiful, durable ceramics. From ancient times to modern day, skilled artisans have harnessed the power of heat to create unique pieces with stunning glazes and surface effects. Speaking of glazes, have you ever wondered about the nutritional facts behind Krispy Kreme's iconic glazed donuts?
Was this page helpful?
Our commitment to delivering trustworthy and engaging content is at the heart of what we do. Each fact on our site is contributed by real users like you, bringing a wealth of diverse insights and information. To ensure the highest standards of accuracy and reliability, our dedicated editors meticulously review each submission. This process guarantees that the facts we share are not only fascinating but also credible. Trust in our commitment to quality and authenticity as you explore and learn with us.