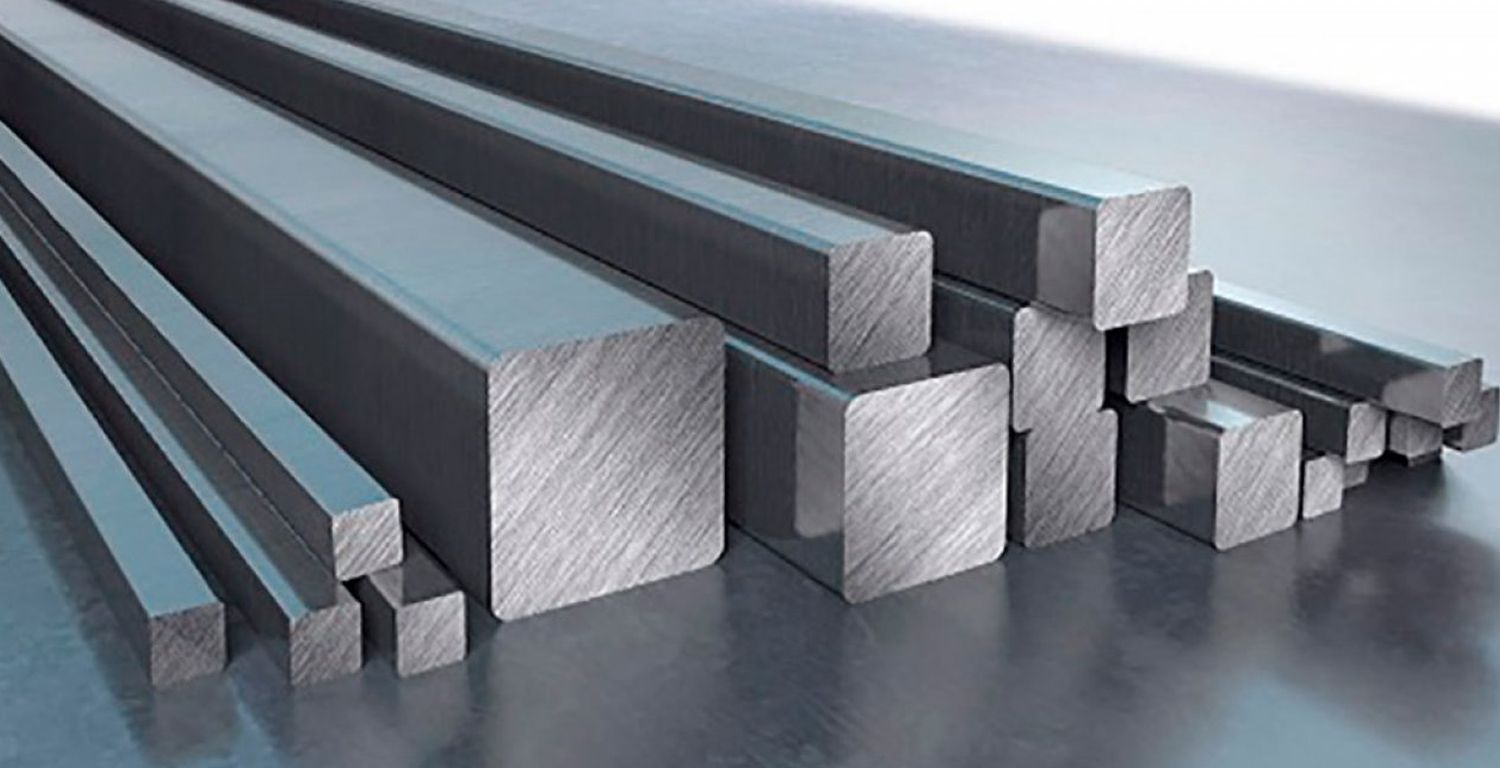
Nimonic alloys are a group of high-performance materials known for their exceptional strength and resistance to heat and corrosion. These superalloys are primarily composed of nickel and chromium, making them ideal for use in extreme environments like jet engines and gas turbines. Nimonic alloys have revolutionized industries by providing reliable performance under intense conditions. But what makes these alloys so special? Nimonic materials offer a unique combination of durability, heat resistance, and corrosion resistance, making them indispensable in aerospace and power generation. In this post, we'll delve into 30 intriguing facts about Nimonic alloys, shedding light on their composition, applications, and the science behind their remarkable properties.
Key Takeaways:
- Nimonic is a family of superalloys known for their strength and resistance to high temperatures. They are used in aerospace, power generation, automotive, medical, and oil and gas industries.
- Despite their advantages, working with Nimonic alloys presents challenges such as high cost, specialized machining, and environmental impact. Innovations and sustainability efforts are ongoing to address these issues.
What is Nimonic?
Nimonic is a family of nickel-based superalloys known for their high-temperature strength and resistance to oxidation and corrosion. These alloys are widely used in the aerospace and power generation industries. Let's dive into some fascinating facts about Nimonic.
Origins and Development
Understanding the history and development of Nimonic can give us insights into its importance and applications.
- Nimonic was first developed in the 1940s by Henry Wiggin & Co. in the UK.
- The name "Nimonic" is derived from "Nickel" and "Monic," indicating its primary composition.
- Initially created for use in gas turbine engines, it has since found applications in various high-stress environments.
- Nimonic alloys were crucial during World War II for improving the performance of jet engines.
- The development of Nimonic alloys marked a significant advancement in materials science, particularly in high-temperature metallurgy.
Composition and Properties
The unique composition of Nimonic alloys gives them their remarkable properties.
- Nimonic alloys typically contain 50-80% nickel, along with chromium, cobalt, and other elements.
- Chromium in Nimonic provides excellent oxidation and corrosion resistance.
- Cobalt enhances the alloy's strength and stability at high temperatures.
- Some Nimonic alloys include aluminum and titanium to improve their mechanical properties.
- These alloys are known for their high creep resistance, making them ideal for prolonged use at elevated temperatures.
Applications of Nimonic
Nimonic's exceptional properties make it suitable for a wide range of applications.
- Nimonic alloys are extensively used in the aerospace industry, particularly in turbine blades and discs.
- They are also used in the power generation sector for gas turbines and nuclear reactors.
- Nimonic is employed in the automotive industry for turbocharger components.
- The oil and gas industry uses Nimonic for drilling equipment and high-pressure valves.
- Medical devices, such as dental implants and surgical instruments, also benefit from Nimonic's properties.
Manufacturing and Processing
The production and processing of Nimonic alloys involve several specialized techniques.
- Nimonic alloys are typically produced through vacuum induction melting to ensure purity.
- They undergo hot and cold working processes to achieve the desired mechanical properties.
- Heat treatment is crucial for enhancing the strength and durability of Nimonic alloys.
- Precision casting is often used to manufacture complex components from Nimonic.
- Advanced machining techniques are required due to the hardness and toughness of Nimonic alloys.
Challenges and Innovations
Despite their advantages, working with Nimonic alloys presents certain challenges.
- The high cost of raw materials like nickel and cobalt makes Nimonic alloys expensive.
- Machining Nimonic requires specialized tools and techniques due to its hardness.
- Welding Nimonic can be challenging because of its tendency to crack under thermal stress.
- Innovations in additive manufacturing are opening new possibilities for producing Nimonic components.
- Research is ongoing to develop new Nimonic alloys with improved properties and lower costs.
Environmental Impact and Sustainability
Considering the environmental impact and sustainability of Nimonic alloys is essential.
- The mining and processing of nickel and cobalt have significant environmental impacts.
- Recycling Nimonic alloys can help reduce the demand for raw materials and lower environmental footprints.
- Advances in green manufacturing techniques aim to make the production of Nimonic more sustainable.
- The long lifespan and durability of Nimonic components contribute to their overall sustainability.
- Efforts are being made to develop eco-friendly alternatives to traditional Nimonic alloys.
The Power of Nimonic
Nimonic alloys are game-changers in high-temperature environments. These superalloys, known for their exceptional strength and resistance to heat, have revolutionized industries like aerospace and power generation. With their nickel-chromium base, they withstand extreme conditions, making them indispensable in jet engines and gas turbines.
Their ability to maintain mechanical properties at high temperatures ensures reliability and longevity. This makes Nimonic alloys a top choice for critical applications where failure is not an option. Their corrosion resistance further enhances their durability, reducing maintenance costs and downtime.
Understanding the unique properties of Nimonic alloys helps us appreciate their role in advancing technology. These materials are not just metals; they are the backbone of modern engineering marvels. So next time you see a jet soaring through the sky, remember the unsung hero, Nimonic, making it all possible.
Frequently Asked Questions
Was this page helpful?
Our commitment to delivering trustworthy and engaging content is at the heart of what we do. Each fact on our site is contributed by real users like you, bringing a wealth of diverse insights and information. To ensure the highest standards of accuracy and reliability, our dedicated editors meticulously review each submission. This process guarantees that the facts we share are not only fascinating but also credible. Trust in our commitment to quality and authenticity as you explore and learn with us.