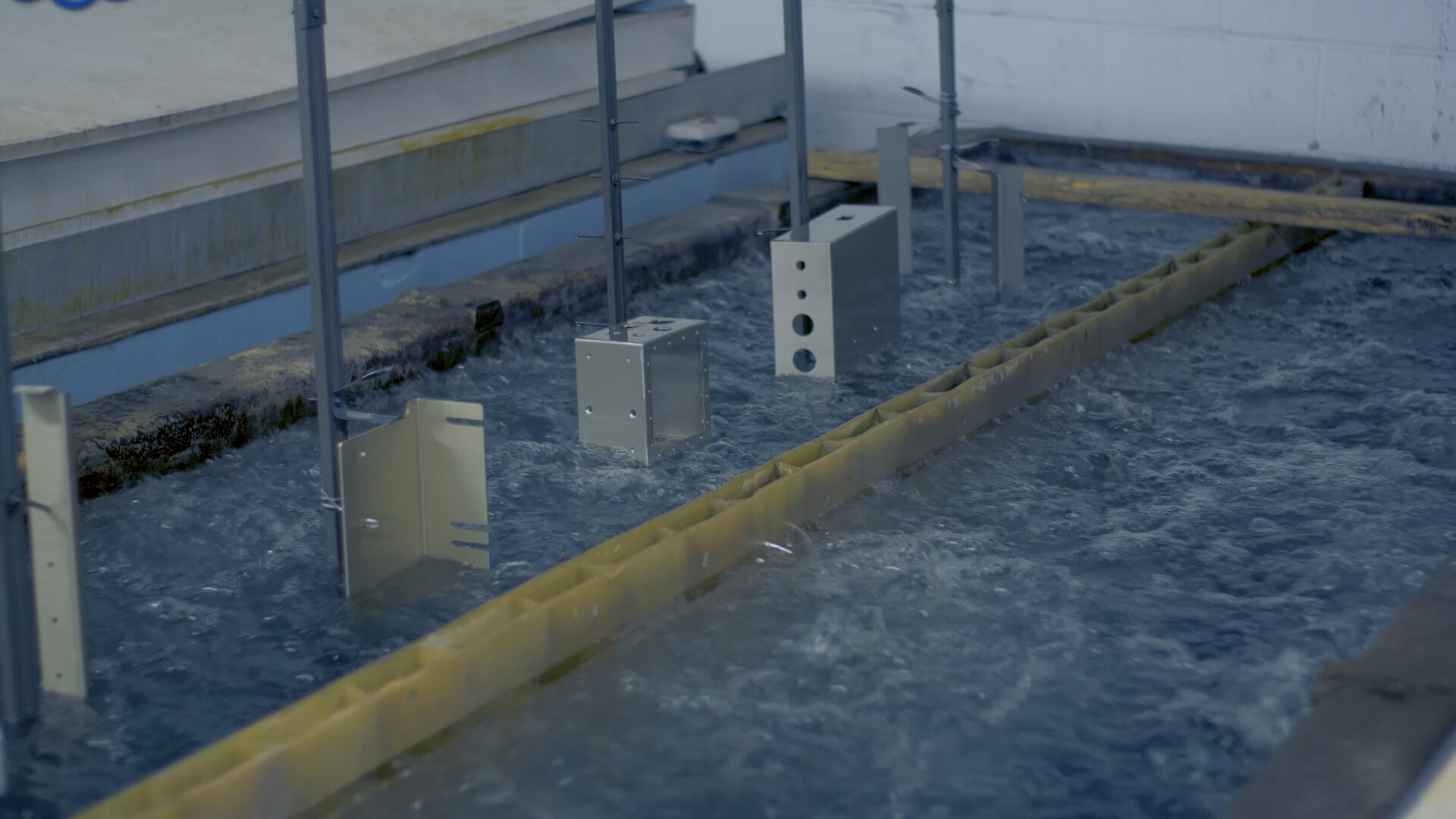
Anodizing is a process that enhances the durability and appearance of metals, especially aluminum. But what exactly happens during anodizing? Anodizing involves creating a protective oxide layer on the metal's surface through an electrochemical process. This layer not only makes the metal more resistant to corrosion and wear but also allows for vibrant coloring. Why should you care about anodizing? It's widely used in industries ranging from aerospace to consumer electronics, ensuring products last longer and look better. Whether you're curious about its environmental impact or its role in everyday items, these 29 facts will give you a deeper understanding of anodizing and its significance.
What is Anodizing?
Anodizing is a process that increases the thickness of the natural oxide layer on the surface of metal parts. This technique is commonly used on aluminum to enhance its durability, appearance, and resistance to corrosion. Let's dive into some fascinating facts about anodizing.
- 01
Anodizing was first developed in the 1920s to protect seaplane parts from corrosion.
- 02
The term "anodizing" comes from the process of using an anode in an electrolytic cell.
- 03
Anodized aluminum can be dyed in various colors, making it popular for decorative purposes.
- 04
The thickness of the anodized layer can range from a few micrometers to over 100 micrometers, depending on the application.
- 05
Anodizing is environmentally friendly because it doesn't involve harmful chemicals.
How Anodizing Works
Understanding the process behind anodizing can help appreciate its benefits. Here are some key points about how anodizing works.
- 06
Anodizing involves immersing the metal in an acid electrolyte bath and passing an electric current through it.
- 07
The metal part acts as the anode, hence the name "anodizing."
- 08
The electric current causes oxygen ions to migrate from the electrolyte to the surface of the metal, forming an oxide layer.
- 09
Sulfuric acid is the most commonly used electrolyte in anodizing aluminum.
- 10
The oxide layer formed during anodizing is porous, allowing for dyeing and sealing.
Benefits of Anodizing
Anodizing offers numerous advantages that make it a preferred choice for various industries. Here are some of the benefits.
- 11
Anodized surfaces are highly resistant to corrosion, extending the lifespan of metal parts.
- 12
The process enhances the metal's aesthetic appeal by allowing for a wide range of colors and finishes.
- 13
Anodized coatings are harder than the base metal, providing increased wear resistance.
- 14
The oxide layer formed during anodizing is non-conductive, making it useful for electrical insulation.
- 15
Anodizing improves the adhesion of paints and adhesives to the metal surface.
Applications of Anodizing
Anodizing is used in a variety of industries due to its versatility and benefits. Here are some common applications.
- 16
Aerospace industry uses anodized aluminum for aircraft parts to prevent corrosion and reduce weight.
- 17
Anodized aluminum is popular in the automotive industry for trim, grills, and other decorative elements.
- 18
Consumer electronics often feature anodized aluminum casings for durability and aesthetics.
- 19
Architectural applications include anodized aluminum for window frames, curtain walls, and roofing.
- 20
Anodized cookware is favored for its non-stick properties and resistance to scratching.
Types of Anodizing
Different types of anodizing processes are used depending on the desired properties and applications. Here are some of the main types.
- 21
Type I anodizing uses chromic acid and is known for its thin, corrosion-resistant coatings.
- 22
Type II anodizing, the most common type, uses sulfuric acid and allows for dyeing and thicker coatings.
- 23
Type III anodizing, also known as hard anodizing, produces very thick and hard coatings for heavy-duty applications.
- 24
Boric-sulfuric acid anodizing is an alternative to chromic acid anodizing, offering similar benefits with less environmental impact.
- 25
Phosphoric acid anodizing is used primarily for adhesive bonding in aerospace applications.
Maintenance and Care for Anodized Surfaces
Proper maintenance can extend the life and appearance of anodized surfaces. Here are some tips for caring for anodized metal.
- 26
Clean anodized surfaces with mild soap and water to remove dirt and grime.
- 27
Avoid using abrasive cleaners or pads, as they can scratch the anodized layer.
- 28
Regularly inspect anodized surfaces for signs of wear or damage and address any issues promptly.
- 29
Apply a protective wax or sealant to maintain the appearance and protect the anodized layer from environmental factors.
The Final Word on Anodizing
Anodizing isn't just a fancy term. It's a game-changer for metals. This process boosts durability, corrosion resistance, and even adds a splash of color. From aerospace to everyday items like smartphones, anodizing plays a crucial role. It’s eco-friendly too, using less harmful chemicals compared to other methods. Plus, it’s cost-effective, making it a popular choice for manufacturers.
Understanding anodizing helps you appreciate the tech behind many products we use daily. Whether it’s your sleek laptop or sturdy bike frame, anodizing makes a difference. So next time you see that shiny, colorful metal, you’ll know the science behind it. Anodizing isn’t just about looks; it’s about making things last longer and perform better. Keep these facts in mind, and you’ll see anodized products in a whole new light.
Was this page helpful?
Our commitment to delivering trustworthy and engaging content is at the heart of what we do. Each fact on our site is contributed by real users like you, bringing a wealth of diverse insights and information. To ensure the highest standards of accuracy and reliability, our dedicated editors meticulously review each submission. This process guarantees that the facts we share are not only fascinating but also credible. Trust in our commitment to quality and authenticity as you explore and learn with us.