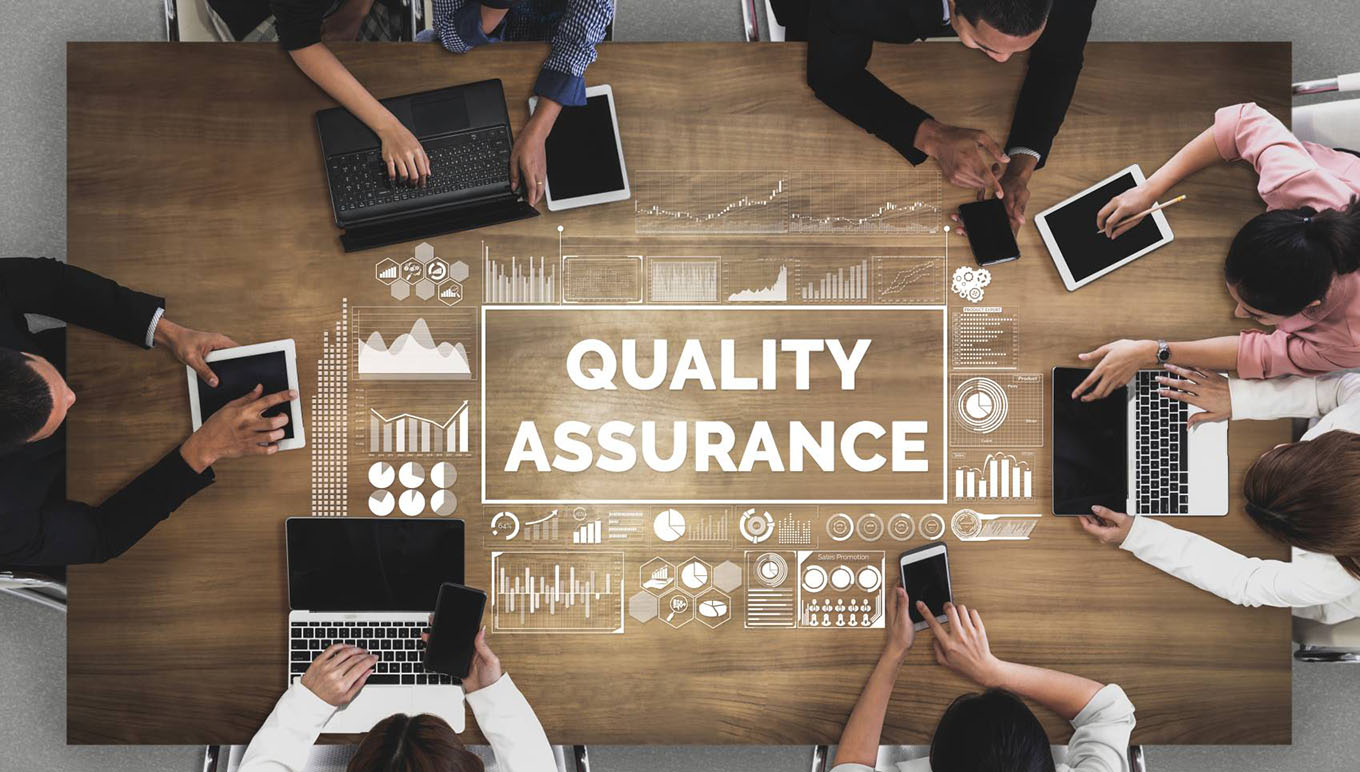
Quality Assurance (QA) is a vital part of any industry, ensuring products and services meet specific standards before reaching consumers. But what exactly does QA involve? Quality Assurance focuses on preventing mistakes and defects in manufactured products and avoiding problems when delivering solutions or services to customers. It’s about maintaining a high level of quality in every aspect of production. From software development to manufacturing, QA plays a crucial role in delivering reliable, high-quality outcomes. This article will dive into 38 fascinating facts about Quality Assurance that highlight its importance, methods, and impact across various fields. Whether you're a student, professional, or just curious, these facts will give you a deeper understanding of how QA shapes the world around us.
Key Takeaways:
- Quality Assurance (QA) ensures products meet standards and promotes continuous improvement. It's crucial in various industries like healthcare, software development, and manufacturing, ensuring safety, reliability, and customer satisfaction.
- QA faces challenges like resource constraints and resistance to change, but the future looks promising with AI, automation, and sustainability shaping its evolution. It's all about ensuring quality, safety, and efficiency in products and services.
What is Quality Assurance?
Quality Assurance (QA) ensures products or services meet specific requirements. It involves systematic activities to guarantee quality in processes and outputs. Here are some intriguing facts about QA.
-
QA vs. QC: Quality Assurance focuses on preventing defects, while Quality Control (QC) identifies defects in finished products.
-
ISO Standards: The International Organization for Standardization (ISO) sets global standards for QA, ensuring consistency and safety.
-
Continuous Improvement: QA promotes continuous improvement, encouraging organizations to constantly enhance their processes.
-
Customer Satisfaction: Effective QA leads to higher customer satisfaction by delivering reliable and high-quality products.
-
Documentation: QA relies heavily on documentation to track processes, changes, and compliance with standards.
The History of Quality Assurance
Understanding the history of QA helps appreciate its evolution and importance in modern industries.
-
Ancient Roots: QA practices date back to ancient civilizations, where craftsmen ensured the quality of their goods.
-
Industrial Revolution: The Industrial Revolution spurred the need for standardized quality practices due to mass production.
-
Shewhart Cycle: Walter A. Shewhart introduced the Plan-Do-Check-Act (PDCA) cycle in the 1920s, a cornerstone of QA.
-
Deming's Influence: W. Edwards Deming's principles revolutionized QA, emphasizing statistical process control and continuous improvement.
-
Total Quality Management (TQM): TQM emerged in the 1980s, integrating QA into every aspect of an organization.
QA in Different Industries
QA practices vary across industries, tailored to specific needs and standards.
-
Manufacturing: In manufacturing, QA ensures products meet specifications and safety standards.
-
Software Development: QA in software involves rigorous testing to identify bugs and ensure functionality.
-
Healthcare: QA in healthcare focuses on patient safety, regulatory compliance, and service quality.
-
Food Industry: QA in food production ensures products are safe, hygienic, and meet regulatory standards.
-
Automotive: The automotive industry uses QA to ensure vehicle safety, reliability, and compliance with regulations.
Tools and Techniques in QA
Various tools and techniques help implement effective QA practices.
-
Six Sigma: Six Sigma uses statistical methods to reduce defects and improve quality.
-
Lean Manufacturing: Lean focuses on minimizing waste while maximizing productivity and quality.
-
Root Cause Analysis: This technique identifies the underlying causes of defects to prevent recurrence.
-
FMEA: Failure Mode and Effects Analysis (FMEA) anticipates potential failures and their impacts.
-
SPC: Statistical Process Control (SPC) monitors and controls processes using statistical methods.
The Role of QA Professionals
QA professionals play a crucial role in maintaining and improving quality standards.
-
QA Managers: They oversee QA processes, ensuring compliance and continuous improvement.
-
QA Analysts: Analysts test products and processes to identify and rectify defects.
-
Auditors: QA auditors assess compliance with standards and regulations through systematic reviews.
-
Trainers: QA trainers educate employees on quality standards and best practices.
-
Consultants: QA consultants provide expert advice to organizations seeking to enhance their QA processes.
Benefits of Quality Assurance
Effective QA offers numerous benefits to organizations and consumers alike.
-
Cost Savings: QA reduces costs by preventing defects and minimizing rework.
-
Brand Reputation: High-quality products enhance brand reputation and customer loyalty.
-
Regulatory Compliance: QA ensures compliance with industry regulations and standards.
-
Risk Management: QA helps identify and mitigate risks, protecting the organization and consumers.
-
Employee Morale: A strong QA culture boosts employee morale by fostering a sense of pride in their work.
Challenges in Quality Assurance
Despite its benefits, QA faces several challenges that organizations must address.
-
Resource Constraints: Limited resources can hinder effective QA implementation.
-
Resistance to Change: Employees may resist new QA processes and standards.
-
Complexity: Complex products and processes require sophisticated QA methods.
-
Globalization: Global supply chains complicate QA due to varying standards and regulations.
-
Technology: Rapid technological advancements necessitate continuous updates to QA practices.
Future of Quality Assurance
The future of QA looks promising, with emerging trends and technologies shaping its evolution.
-
AI and Automation: AI and automation streamline QA processes, enhancing efficiency and accuracy.
-
Big Data: Big data analytics provide insights into quality trends and potential issues.
-
Sustainability: QA increasingly focuses on sustainability, ensuring products are environmentally friendly and socially responsible.
Final Thoughts on Quality Assurance
Quality assurance (QA) isn't just a buzzword; it's a vital part of any successful project. Ensuring products meet high standards, QA helps catch issues early, saving time and money. It involves various methods like manual testing, automated testing, and user acceptance testing. Each plays a role in delivering a reliable product. QA also boosts customer satisfaction by providing a seamless user experience. Teams that prioritize QA often see fewer bugs, better performance, and happier users.
QA isn't just for tech giants; small businesses benefit too. Investing in QA can lead to long-term success. So, whether you're a startup or an established company, don't skimp on quality assurance. It’s a smart move that pays off in the long run. Keep these facts in mind, and you'll be well on your way to delivering top-notch products.
Frequently Asked Questions
Was this page helpful?
Our commitment to delivering trustworthy and engaging content is at the heart of what we do. Each fact on our site is contributed by real users like you, bringing a wealth of diverse insights and information. To ensure the highest standards of accuracy and reliability, our dedicated editors meticulously review each submission. This process guarantees that the facts we share are not only fascinating but also credible. Trust in our commitment to quality and authenticity as you explore and learn with us.