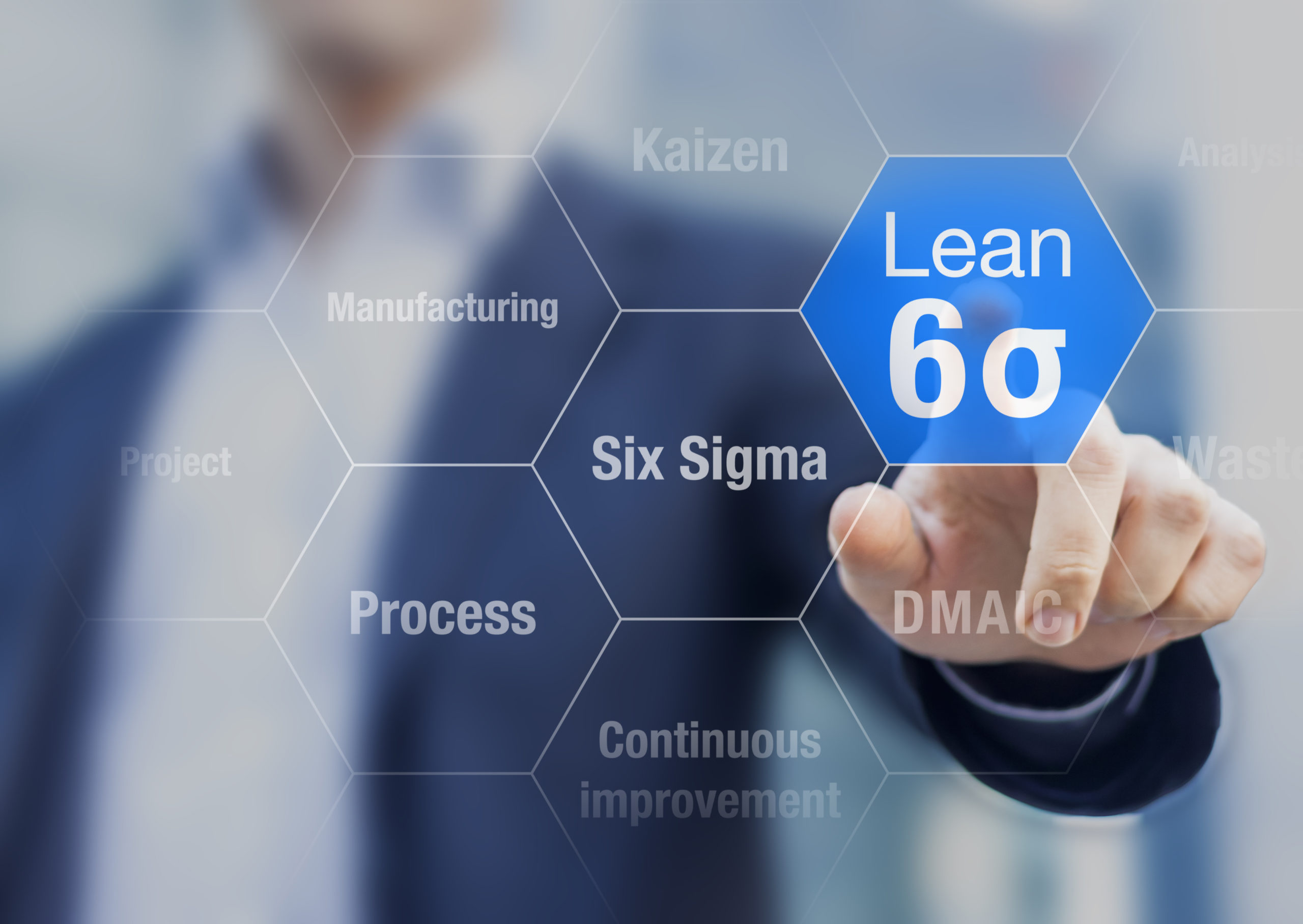
What is Six Sigma? Six Sigma is a methodology that aims to improve business processes by reducing defects and variability. Developed by Motorola in the 1980s, it uses statistical tools and techniques to identify and eliminate errors. Why is it important? Because it helps companies save money, improve quality, and increase customer satisfaction. How does it work? Six Sigma follows a structured approach known as DMAIC: Define, Measure, Analyze, Improve, and Control. Who uses it? Many industries, from manufacturing to healthcare, utilize Six Sigma to streamline operations. What are the benefits? Enhanced efficiency, reduced costs, and better product quality. Is it hard to learn? Not necessarily; with proper training and dedication, anyone can grasp its concepts. Ready to dive into 25 fascinating facts about Six Sigma? Let’s get started!
Key Takeaways:
- Six Sigma is a powerful method for improving quality and reducing defects in processes. It uses data-driven decisions and various tools like Pareto charts and control charts to make processes more efficient.
- Companies like GE, Motorola, and Ford have successfully used Six Sigma to save money, improve quality, and gain a competitive edge. It's not just for manufacturing; it's also used in healthcare, finance, IT, and customer service.
What is Six Sigma?
Six Sigma is a set of techniques and tools for process improvement. It was introduced by engineer Bill Smith while working at Motorola in 1986. The goal is to improve the quality of process outputs by identifying and removing the causes of defects and minimizing variability in manufacturing and business processes.
-
Origin: Six Sigma was developed by Motorola in 1986 to improve manufacturing processes and reduce defects.
-
Meaning: The term "Six Sigma" comes from statistics and refers to a process that is six standard deviations from the mean, ensuring near-perfect quality.
-
Certification Levels: Six Sigma has different certification levels, similar to martial arts belts: White, Yellow, Green, Black, and Master Black Belt.
-
DMAIC: The core methodology of Six Sigma is DMAIC, which stands for Define, Measure, Analyze, Improve, and Control.
-
DMADV: Another methodology used in Six Sigma is DMADV, which stands for Define, Measure, Analyze, Design, and Verify, often used for new processes.
Benefits of Six Sigma
Implementing Six Sigma can bring numerous benefits to organizations, from cost savings to improved customer satisfaction. Here are some key advantages.
-
Cost Reduction: Six Sigma helps in identifying waste and inefficiencies, leading to significant cost reductions.
-
Customer Satisfaction: By improving quality and reducing defects, Six Sigma enhances customer satisfaction and loyalty.
-
Employee Engagement: Six Sigma projects often involve team collaboration, boosting employee engagement and morale.
-
Competitive Advantage: Companies that implement Six Sigma can gain a competitive edge by delivering higher quality products and services.
-
Data-Driven Decisions: Six Sigma relies on data and statistical analysis, leading to more informed and effective decision-making.
Tools and Techniques
Six Sigma employs a variety of tools and techniques to analyze and improve processes. These tools help in identifying problems and finding solutions.
-
Pareto Chart: A Pareto Chart helps identify the most significant factors in a dataset, based on the Pareto Principle (80/20 rule).
-
Fishbone Diagram: Also known as the Ishikawa or cause-and-effect diagram, it helps identify root causes of problems.
-
Control Charts: These charts monitor process performance over time and help in maintaining control.
-
Failure Mode and Effects Analysis (FMEA): FMEA identifies potential failure points in a process and their impact, helping to prioritize improvements.
-
SIPOC Diagram: SIPOC stands for Suppliers, Inputs, Process, Outputs, and Customers, providing a high-level view of a process.
Real-World Applications
Six Sigma is not limited to manufacturing; it has been successfully applied in various industries. Here are some examples.
-
Healthcare: Six Sigma has been used to reduce patient wait times, improve patient care, and streamline hospital processes.
-
Finance: Financial institutions use Six Sigma to improve transaction accuracy, reduce errors, and enhance customer service.
-
IT and Software Development: In IT, Six Sigma helps in improving software quality, reducing bugs, and enhancing project management.
-
Supply Chain Management: Six Sigma optimizes supply chain processes, reducing lead times and improving inventory management.
-
Customer Service: Companies use Six Sigma to enhance customer service processes, leading to quicker resolution times and higher satisfaction.
Famous Companies Using Six Sigma
Many well-known companies have adopted Six Sigma to improve their operations. Here are some notable examples.
-
General Electric (GE): Under the leadership of Jack Welch, GE saved billions of dollars by implementing Six Sigma.
-
Motorola: As the birthplace of Six Sigma, Motorola has seen significant improvements in quality and efficiency.
-
Honeywell: Honeywell has used Six Sigma to streamline operations and improve product quality.
-
Ford: Ford Motor Company has applied Six Sigma to enhance manufacturing processes and reduce defects.
-
3M: 3M has utilized Six Sigma to drive innovation and improve product development processes.
The Power of Six Sigma
Six Sigma isn't just a buzzword. It's a powerful methodology that can transform businesses. By focusing on reducing defects and improving processes, companies can save money, boost efficiency, and enhance customer satisfaction. Whether you're in manufacturing, healthcare, or even finance, Six Sigma principles apply across various industries.
Understanding its core concepts like DMAIC (Define, Measure, Analyze, Improve, Control) and DMADV (Define, Measure, Analyze, Design, Verify) can give you a competitive edge. Plus, the different belt levels—Yellow, Green, Black, and Master Black—offer a clear path for professional growth.
So, if you're looking to make a significant impact in your organization, diving into Six Sigma might just be the game-changer you need. Embrace the data-driven approach and watch your processes improve dramatically.
Frequently Asked Questions
Was this page helpful?
Our commitment to delivering trustworthy and engaging content is at the heart of what we do. Each fact on our site is contributed by real users like you, bringing a wealth of diverse insights and information. To ensure the highest standards of accuracy and reliability, our dedicated editors meticulously review each submission. This process guarantees that the facts we share are not only fascinating but also credible. Trust in our commitment to quality and authenticity as you explore and learn with us.