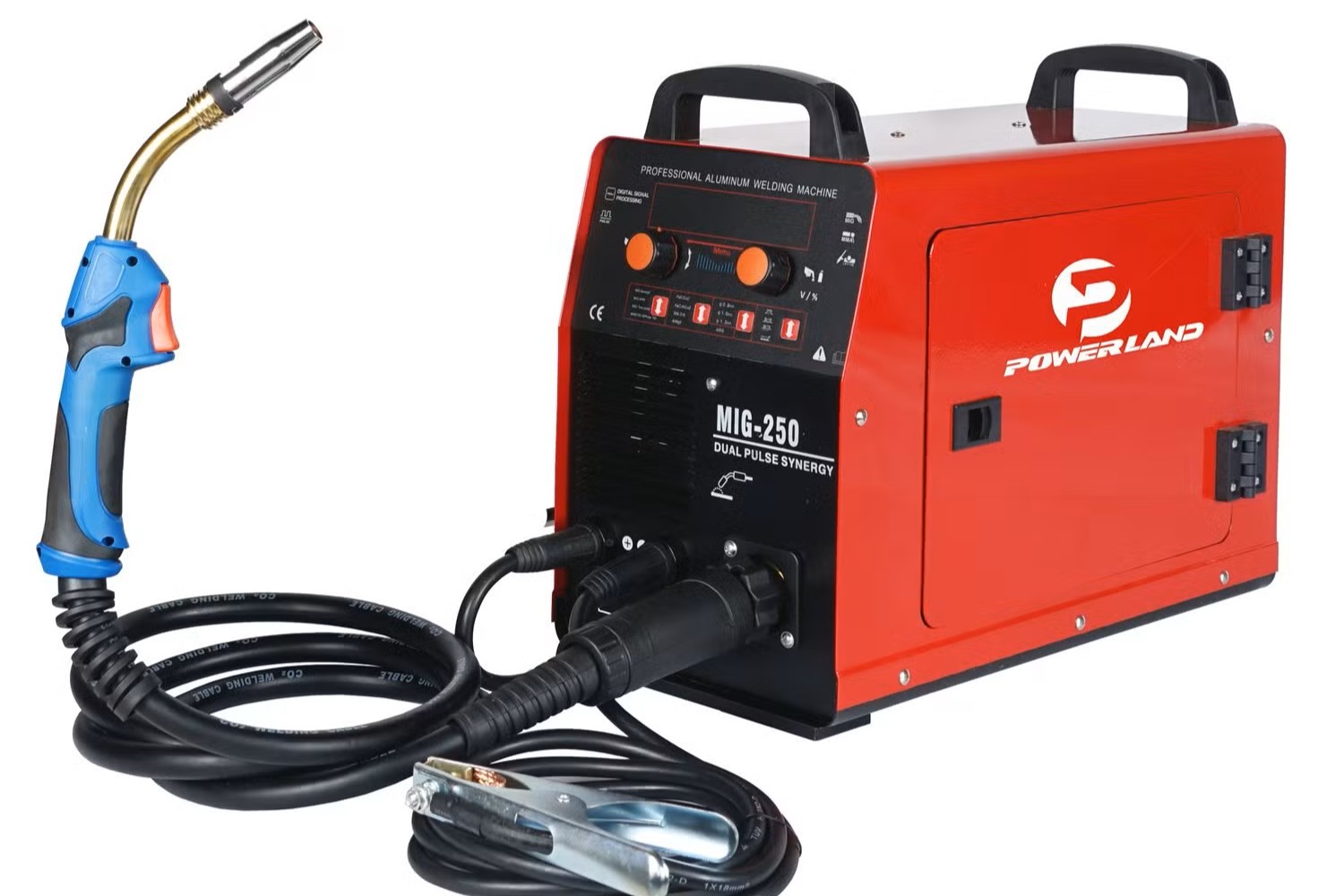
What makes a MIG welder special? MIG welding, or Metal Inert Gas welding, is a popular technique in the world of metalwork. MIG welders are known for their ease of use, making them a favorite among both beginners and professionals. They use a continuous wire feed as an electrode and a shielding gas to protect the weld from contamination. This method allows for cleaner, more precise welds on various metals like steel, aluminum, and stainless steel. MIG welding is also faster compared to other welding methods, boosting productivity. Whether you're fixing a car, building a sculpture, or working on a construction project, a MIG welder can be your best friend in achieving strong, durable welds.
What is MIG Welding?
MIG welding, or Metal Inert Gas welding, is a popular welding technique used in various industries. It involves using a continuous wire electrode and a shielding gas to protect the weld from contamination. Here are some interesting facts about MIG welders.
-
MIG stands for Metal Inert Gas. This welding process uses an inert gas to shield the weld pool from atmospheric contamination.
-
Invented in the 1940s. MIG welding was developed during World War II to increase the speed and efficiency of welding processes.
-
Uses a continuous wire feed. Unlike other welding methods, MIG welding employs a continuous wire electrode that is fed through the welding gun.
-
Suitable for various metals. MIG welding can be used on a wide range of metals, including aluminum, stainless steel, and carbon steel.
-
Requires a shielding gas. Common shielding gases include argon, carbon dioxide, or a mixture of both, which protect the weld from oxidation and contamination.
Advantages of MIG Welding
MIG welding offers several benefits that make it a preferred choice for many welders. Let's explore some of these advantages.
-
High welding speed. The continuous wire feed allows for faster welding compared to other methods.
-
Ease of use. MIG welding is relatively easy to learn, making it accessible for beginners.
-
Versatility. This welding technique can be used in various positions, including flat, horizontal, vertical, and overhead.
-
Cleaner welds. The shielding gas reduces the amount of slag and spatter, resulting in cleaner welds.
-
Minimal post-weld cleanup. Due to the reduced spatter, there is less need for extensive post-weld cleaning.
Applications of MIG Welding
MIG welding is used in a variety of industries and applications. Here are some examples of where this welding technique is commonly employed.
-
Automotive industry. MIG welding is widely used in the manufacturing and repair of vehicles.
-
Construction. This welding method is often used in the construction of buildings, bridges, and other structures.
-
Shipbuilding. MIG welding is essential in the construction and repair of ships and other marine vessels.
-
Aerospace. The aerospace industry relies on MIG welding for the fabrication of aircraft components.
-
Manufacturing. MIG welding is used in the production of various consumer goods and industrial equipment.
Safety Considerations for MIG Welding
Safety is crucial when performing MIG welding. Here are some important safety tips to keep in mind.
-
Wear appropriate protective gear. This includes a welding helmet, gloves, and flame-resistant clothing.
-
Ensure proper ventilation. Welding fumes can be hazardous, so it's important to work in a well-ventilated area.
-
Check equipment regularly. Inspect the welding machine, cables, and connections for any signs of damage or wear.
-
Avoid flammable materials. Keep the welding area free of flammable materials to prevent fires.
-
Follow safety guidelines. Always adhere to safety guidelines and best practices to minimize the risk of accidents.
Common Issues in MIG Welding
Even with its advantages, MIG welding can present some challenges. Here are a few common issues welders might encounter.
-
Porosity. This occurs when gas gets trapped in the weld, leading to weak spots.
-
Burnback. This happens when the wire electrode melts into the contact tip, causing the welding process to stop.
-
Wire feed problems. Issues with the wire feed can result in inconsistent welds.
-
Spatter. Although MIG welding produces less spatter than other methods, it can still be an issue if not properly managed.
-
Inadequate penetration. This occurs when the weld does not penetrate deeply enough into the base material, leading to weak joints.
Tips for Improving MIG Welding Skills
Improving your MIG welding skills can lead to better welds and increased efficiency. Here are some tips to help you get better at MIG welding.
-
Practice regularly. Consistent practice is key to mastering MIG welding techniques.
-
Adjust settings. Experiment with different settings on your welding machine to find the optimal parameters for your project.
-
Maintain equipment. Regularly clean and maintain your welding equipment to ensure optimal performance.
-
Seek feedback. Get feedback from experienced welders to identify areas for improvement and refine your skills.
Welding Wonders
MIG welders are pretty amazing, right? They’re versatile, easy to use, and perfect for beginners and pros alike. From automotive repairs to artistic metalwork, these machines handle a wide range of tasks. Knowing the different types of MIG welders and their features can help you pick the right one for your projects.
Remember, safety first! Always wear protective gear and follow guidelines to avoid accidents. Regular maintenance keeps your welder in top shape, ensuring smooth and efficient operation.
Whether you’re fixing a broken gate or crafting a metal sculpture, a MIG welder is a trusty companion. With the right knowledge and tools, you can tackle any welding project with confidence. So, get out there and start welding!
Was this page helpful?
Our commitment to delivering trustworthy and engaging content is at the heart of what we do. Each fact on our site is contributed by real users like you, bringing a wealth of diverse insights and information. To ensure the highest standards of accuracy and reliability, our dedicated editors meticulously review each submission. This process guarantees that the facts we share are not only fascinating but also credible. Trust in our commitment to quality and authenticity as you explore and learn with us.