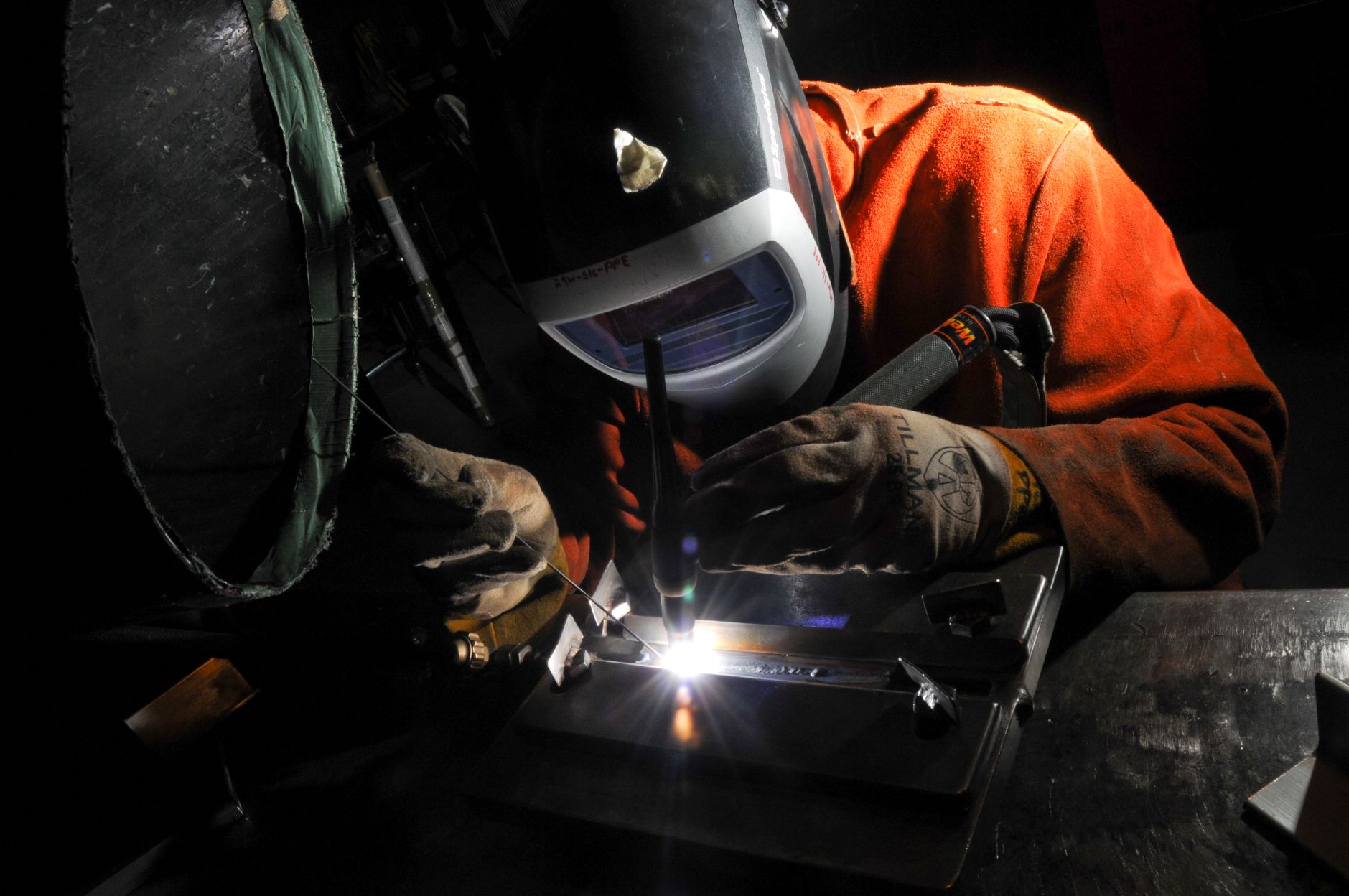
Tig welding, also known as Gas Tungsten Arc Welding (GTAW), is a popular welding process that offers precise control and high-quality welds. Whether you’re a seasoned welder or just starting to explore the world of welding, it’s crucial to have a good understanding of the facts surrounding Tig welding.
In this article, we will dive into 19 Tig welding facts that will not only increase your knowledge but also help you optimize your welding techniques. From understanding the basics of Tig welding to exploring its advantages and applications, these facts will equip you with valuable insights to become a proficient Tig welder.
So, keep your welding helmet on, grab your gloves, and let’s embark on this Tig welding adventure!
Key Takeaways:
- Tig welding is a precise and versatile process used in various industries, offering clean and strong welds for a wide range of materials.
- With Tig welding, skilled welders can create intricate welds with minimal distortion, making it ideal for critical applications and automated welding systems.
Tig welding, also known as Gas Tungsten Arc Welding (GTAW), is a versatile welding process that offers precision and control.
Tig welding is widely used in various industries, including automotive, aerospace, and fabrication. It utilizes a non-consumable tungsten electrode to create the weld, which makes it ideal for welding thin materials and producing high-quality welds.
Tig welding requires a shielding gas to protect the weld pool and electrode from contamination.
Argon is commonly used as a shielding gas in Tig welding due to its inert properties. It ensures a clean and stable arc, resulting in strong and aesthetically pleasing welds.
One of the significant advantages of Tig welding is its ability to weld a wide range of metals.
From stainless steel and aluminum to copper and titanium, Tig welding is suitable for welding both ferrous and non-ferrous metals. This makes it a preferred choice for various applications in different industries.
Precision and control are the hallmark of Tig welding.
The welder has precise control over the heat input, welding speed, and filler metal deposition. This enables them to create intricate welds with minimal distortion and exceptional weld quality.
Tig welding can be performed in various positions, including flat, horizontal, vertical, and overhead.
With the right technique and skill, Tig welding can be done in any position, allowing for versatility and flexibility in welding different parts and structures.
Tig welding produces clean and aesthetically pleasing welds.
Due to the precise control over the weld pool, Tig welding produces welds with minimal spatter, porosity, and discontinuities. This results in visually appealing welds that require minimal post-weld cleanup.
Tig welding is commonly used for welding thin materials.
Being able to control the heat input and weld pool size, Tig welding is ideal for welding materials as thin as 0.015 inches. It is often used in applications such as sheet metal fabrication, pipe welding, and small-scale component welding.
The Tig welding process requires a high level of skill and expertise.
As Tig welding demands precise control and technique, welders undergo extensive training and practice to master the process. It takes time and experience to achieve consistent and high-quality welds.
Tig welding offers excellent arc visibility.
Unlike other welding processes, Tig welding produces a focused and concentrated arc. This improves visibility during the welding process, allowing the welder to have better control over the weld pool and produce accurate welds.
Tig welding can be performed using either direct current (DC) or alternating current (AC).
DC Tig welding is commonly used for welding stainless steel, aluminum, and other non-ferrous metals. AC Tig welding, on the other hand, is suitable for welding aluminum and magnesium alloys, as it helps to clean the oxide layer while welding.
Tig welding can be done with or without filler metal.
When joining two pieces of metal, a filler metal is typically added to create a stronger bond. However, Tig welding can also be performed without filler metal, known as autogenous welding, in certain applications.
Tig welding allows for precise control over the weld puddle size.
The welder can adjust the amperage, travel speed, and filler metal deposition to control the size of the weld puddle. This enables them to match the weld size to the requirements of the application.
Tig welding is a relatively slow welding process.
Due to the precision and control required, Tig welding is slower compared to other welding processes. However, the slower speed allows for better control over the weld and reduces the risk of overheating the material.
Tig welding can produce welds with exceptional strength and durability.
With proper welding techniques and adequate penetration, Tig welding can create welds that have high tensile strength and excellent structural integrity. This makes it suitable for critical applications where weld quality is essential.
Tig welding can be used for welding exotic metals like titanium.
Titanium is a challenging material to weld due to its high melting point and reactivity to oxygen. However, Tig welding with precise control over shielding gas and heat input allows for successful welding of titanium and other exotic metals.
Tig welding is a versatile process for both manual and automated welding.
While Tig welding is often associated with manual welding, it can also be used in automated welding systems. This allows for consistent and repeatable welds in high-production environments.
Tig welding requires a high-frequency starting mechanism.
A high-frequency start provides a smooth and controlled arc initiation, preventing the tungsten electrode from sticking to the workpiece. This feature is essential for achieving clean and precise weld starts.
Tig welding produces minimal distortion in the welded material.
The focused heat input and precise control over the weld pool minimize the heat-affected zone. This results in minimal distortion and warping, making Tig welding suitable for welding critical components and structures.
Tig welding is often used for welding pipes and tubing.
Due to its ability to weld thin materials and produce clean welds, Tig welding is commonly used in pipe and tubing applications, including plumbing, HVAC systems, and automotive exhaust systems.
Conclusion
In conclusion, these 19 Tig Welding Facts provide valuable insights into the world of Tig welding. From its history and benefits to the techniques and equipment involved, Tig welding is a complex and precise process that requires skill and practice. Whether you are a hobbyist or a professional welder, understanding these facts will help you improve your welding skills and produce high-quality welds. So, start exploring the fascinating world of Tig welding and unleash your creativity!
FAQs
Q: What does TIG stand for in Tig Welding?
A: TIG stands for Tungsten Inert Gas.
Q: Can I use Tig welding on all types of metals?
A: Yes, Tig welding is suitable for a wide range of metals including stainless steel, aluminum, copper, and more.
Q: How does Tig welding differ from other welding processes?
A: Tig welding uses a non-consumable tungsten electrode and an inert gas shield, resulting in a cleaner and more precise weld compared to other processes.
Q: Is Tig welding difficult to learn?
A: Tig welding can be challenging to learn due to the level of skill and control required, but with practice and guidance, anyone can become proficient in Tig welding.
Q: Can Tig welding be used for thin materials?
A: Yes, Tig welding is highly suitable for welding thin materials as it provides precise control over the heat input, minimizing the risk of distortion or damage.
Q: What safety precautions should I take when Tig welding?
A: It is important to wear protective gear, such as welding gloves, a welding helmet, and flame-resistant clothing. Adequate ventilation and eye protection are also essential.
Q: Can Tig welding be automated?
A: Yes, Tig welding can be automated using robotic systems, allowing for consistent and high-speed production in industries such as automotive and manufacturing.
Q: What is the advantage of using a foot pedal in Tig welding?
A: The foot pedal allows welders to control the amperage during the welding process, giving them greater control over the heat input and weld bead appearance.
Q: Does Tig welding produce a stronger weld compared to other welding processes?
A: Tig welding can produce strong and high-quality welds when performed correctly, but the strength of the weld also depends on other factors such as material selection and joint preparation.
Q: Is Tig welding more expensive than other welding processes?
A: Tig welding equipment and consumables can be more expensive compared to other welding processes, but the investment is worth it considering the precision and quality of the welds produced.
Tig welding offers precision, versatility, and exceptional results. Mastering this skill requires practice, patience, and the right equipment. Selecting a high-quality welding helmet is essential for protecting eyes and ensuring clear visibility during welding tasks. Investing in a reliable helmet can make all the difference in comfort, safety, and weld quality.
Was this page helpful?
Our commitment to delivering trustworthy and engaging content is at the heart of what we do. Each fact on our site is contributed by real users like you, bringing a wealth of diverse insights and information. To ensure the highest standards of accuracy and reliability, our dedicated editors meticulously review each submission. This process guarantees that the facts we share are not only fascinating but also credible. Trust in our commitment to quality and authenticity as you explore and learn with us.