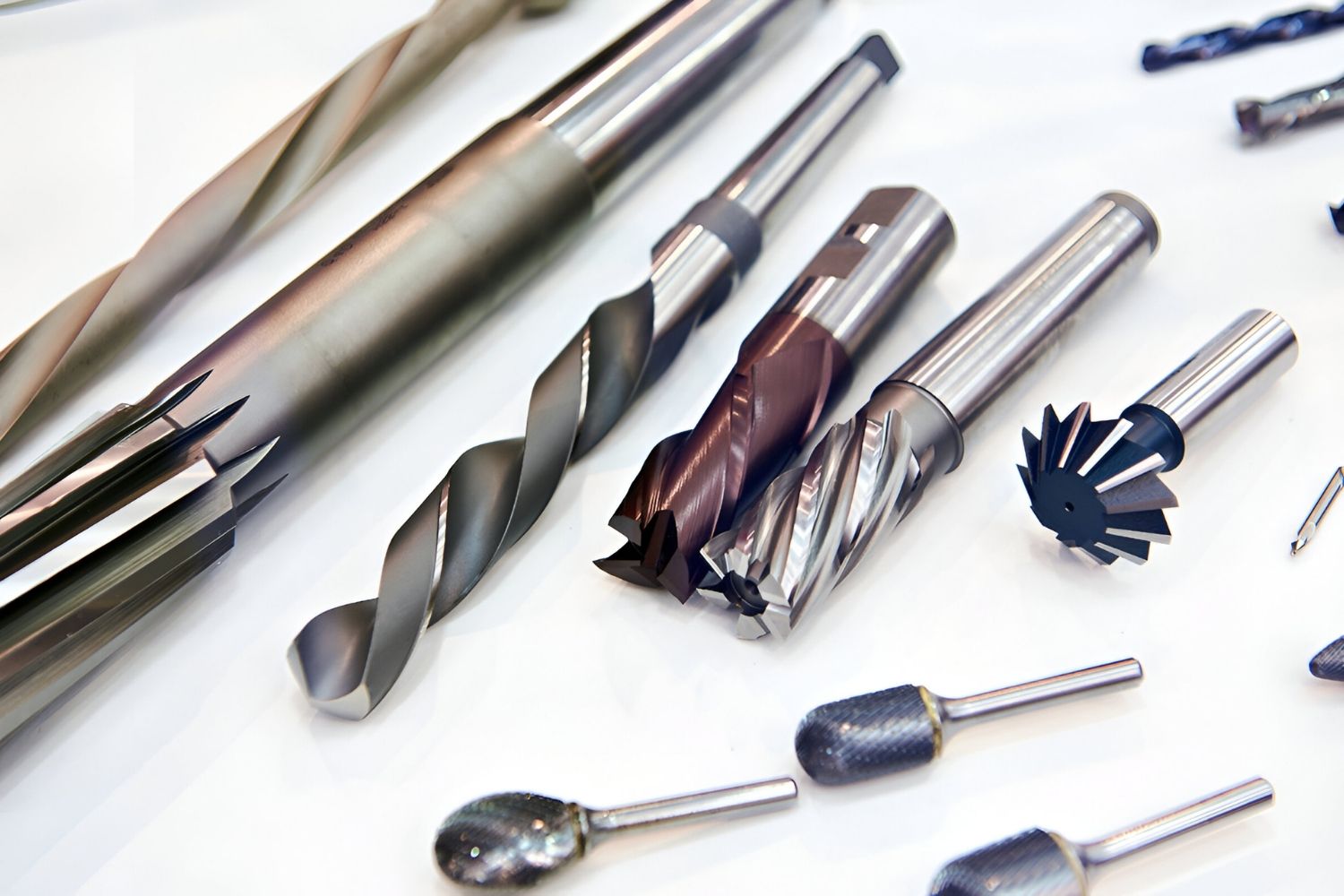
Tool steel is a type of carbon and alloy steel known for its hardness, resistance to abrasion, and ability to hold a cutting edge. This makes it perfect for manufacturing tools, dies, and machine parts. But what exactly sets tool steel apart from other types of steel? Tool steel contains varying amounts of tungsten, molybdenum, cobalt, and vanadium, which contribute to its unique properties. These elements allow the steel to withstand high temperatures and maintain its shape under stress. Whether you're a budding blacksmith, a seasoned machinist, or just curious about materials science, understanding tool steel can be incredibly beneficial. Let's dive into 50 fascinating facts about this remarkable material!
Key Takeaways:
- Tool steel is a super tough and durable type of steel used for making tools and dies. It can be heat-treated to be even harder and is great for cutting and shaping materials.
- Tool steel comes in different types, each designed for specific jobs like cutting tools, molds, and knives. It's super strong and can withstand high temperatures, making it perfect for tough jobs.
What is Tool Steel?
Tool steel is a type of carbon and alloy steel known for its hardness, resistance to abrasion, and ability to hold a cutting edge. These properties make it ideal for manufacturing tools and dies.
- 01Tool steel contains varying amounts of carbon, typically ranging from 0.5% to 1.5%.
- 02It is often alloyed with elements like tungsten, molybdenum, vanadium, and chromium to enhance its properties.
- 03The high carbon content gives tool steel its hardness and strength.
- 04Tool steel is used in applications requiring high wear resistance and toughness.
- 05It can be heat-treated to achieve different levels of hardness and durability.
Types of Tool Steel
There are several types of tool steel, each designed for specific applications. Understanding these types helps in selecting the right material for the job.
- 06Water-Hardening Tool Steel (W-Series): This type is quenched in water and is the most basic form of tool steel.
- 07Cold-Work Tool Steel: Used for cutting and shaping materials at room temperature.
- 08Shock-Resistant Tool Steel (S-Series): Designed to withstand impact and shock loading.
- 09Hot-Work Tool Steel (H-Series): Suitable for high-temperature applications.
- 10High-Speed Tool Steel (T-Series and M-Series): Maintains hardness at high temperatures, ideal for cutting tools.
Applications of Tool Steel
Tool steel's unique properties make it suitable for a wide range of applications. Here are some common uses.
- 11Cutting Tools: Used to make drills, taps, and milling cutters.
- 12Molds: Essential in the production of plastic injection molds.
- 13Dies: Utilized in stamping and forming dies.
- 14Knives: High-quality kitchen and industrial knives are often made from tool steel.
- 15Punches: Used in punching and blanking operations.
Properties of Tool Steel
Tool steel is known for its exceptional properties, which make it ideal for demanding applications.
- 16Hardness: Tool steel can be extremely hard, making it resistant to wear.
- 17Toughness: Despite its hardness, it can also be tough, resisting chipping and cracking.
- 18Heat Resistance: Some types can withstand high temperatures without losing hardness.
- 19Wear Resistance: Excellent wear resistance ensures long-lasting performance.
- 20Machinability: Can be machined to precise dimensions and shapes.
Heat Treatment of Tool Steel
Heat treatment is a crucial process in enhancing the properties of tool steel. It involves heating and cooling the steel to achieve desired characteristics.
- 21Annealing: Softens the steel for easier machining.
- 22Hardening: Increases hardness by heating and then rapidly cooling the steel.
- 23Tempering: Reduces brittleness while maintaining hardness.
- 24Quenching: Rapid cooling in water, oil, or air to harden the steel.
- 25Stress Relieving: Reduces internal stresses caused by machining or heat treatment.
Advantages of Tool Steel
Tool steel offers several advantages that make it a preferred choice for many industrial applications.
- 26Durability: Long-lasting performance even under harsh conditions.
- 27Precision: Can be machined to very tight tolerances.
- 28Versatility: Suitable for a wide range of applications.
- 29Cost-Effective: Long lifespan reduces the need for frequent replacements.
- 30Customizable: Properties can be tailored through alloying and heat treatment.
Challenges with Tool Steel
Despite its many advantages, tool steel also presents some challenges that need to be addressed.
- 31Cost: Higher initial cost compared to other types of steel.
- 32Machining Difficulty: Hardness can make machining more challenging.
- 33Heat Treatment Sensitivity: Requires precise control during heat treatment.
- 34Corrosion: Some types are prone to rust if not properly maintained.
- 35Brittleness: Can be brittle if not properly tempered.
Innovations in Tool Steel
Recent advancements have led to the development of new types of tool steel with improved properties.
- 36Powder Metallurgy: Produces tool steel with a more uniform microstructure.
- 37Cryogenic Treatment: Enhances wear resistance and toughness.
- 38Coatings: Applying coatings like titanium nitride improves performance.
- 39Nanostructured Tool Steel: Offers superior hardness and toughness.
- 40Recycling: Advances in recycling techniques make tool steel more sustainable.
Tool Steel in Different Industries
Tool steel is used across various industries due to its unique properties. Here are some examples.
- 41Automotive: Used in the manufacturing of engine components and body panels.
- 42Aerospace: Essential for making high-stress components like landing gear.
- 43Construction: Utilized in tools and machinery for building and infrastructure projects.
- 44Medical: Used in surgical instruments and medical devices.
- 45Energy: Important in the production of oil and gas drilling equipment.
Maintenance of Tool Steel
Proper maintenance is crucial to extend the lifespan of tool steel tools and components.
The Final Word on Tool Steel
Tool steel is a fascinating material with a rich history and a wide range of applications. From its high carbon content to its incredible hardness, tool steel stands out in the world of metallurgy. Whether you're a machinist, blacksmith, or just a curious reader, understanding these facts can deepen your appreciation for this versatile metal.
Remember, tool steel isn't just one type; it includes various grades like A2, D2, and O1, each with unique properties. Its ability to withstand high temperatures and abrasion makes it indispensable in manufacturing and construction.
So next time you see a cutting tool or mold, you'll know the science and craftsmanship behind it. Keep exploring, stay curious, and never underestimate the power of a well-crafted tool.
Frequently Asked Questions
Was this page helpful?
Our commitment to delivering trustworthy and engaging content is at the heart of what we do. Each fact on our site is contributed by real users like you, bringing a wealth of diverse insights and information. To ensure the highest standards of accuracy and reliability, our dedicated editors meticulously review each submission. This process guarantees that the facts we share are not only fascinating but also credible. Trust in our commitment to quality and authenticity as you explore and learn with us.