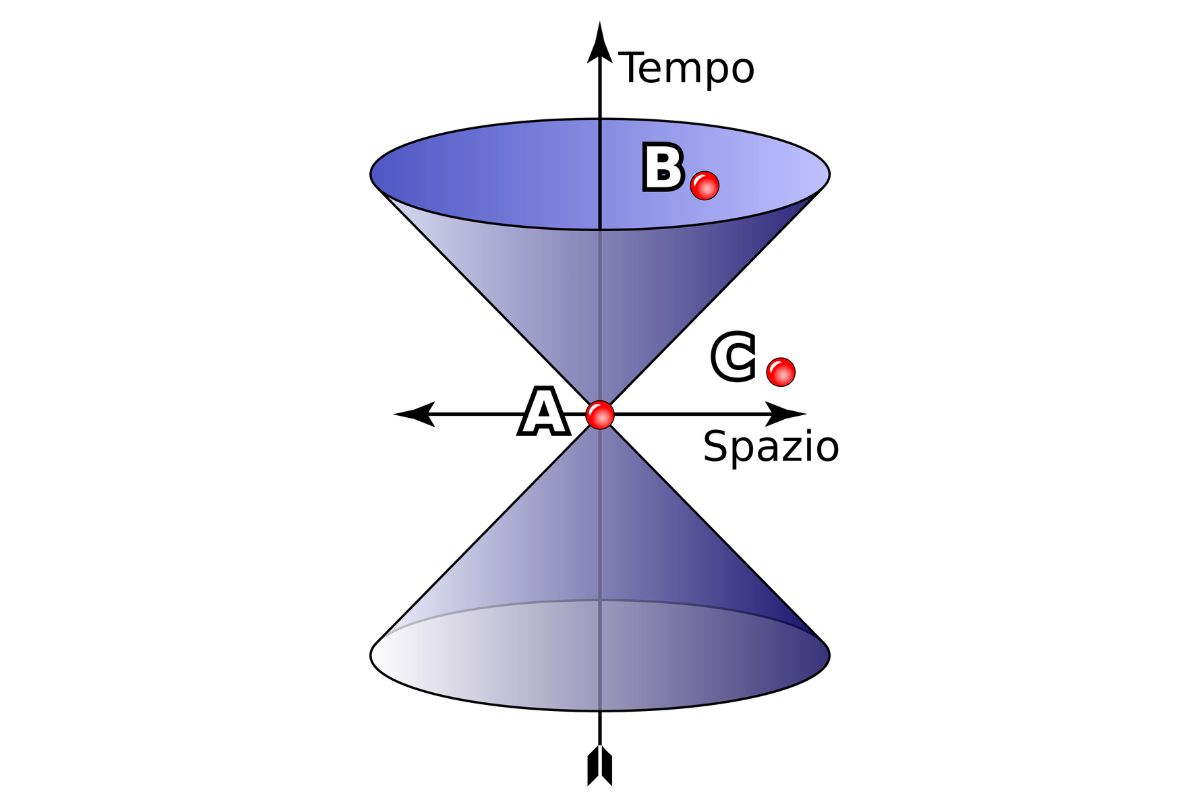
Conformal coatings are essential in protecting electronic circuits from harsh environments. But what exactly are they, and why are they so crucial? Conformal coatings are thin layers of protective material applied to electronic components to guard against moisture, dust, chemicals, and temperature extremes. These coatings ensure the longevity and reliability of electronic devices, making them indispensable in industries like aerospace, automotive, and consumer electronics. With various types available, such as acrylic, silicone, and polyurethane, each offers unique benefits tailored to specific needs. Understanding the importance and application of conformal coatings can help you make informed decisions about protecting your electronic investments. Ready to dive into 35 fascinating facts about these protective marvels? Let's get started!
What is Conformal Coating?
Conformal coating is a protective chemical layer applied to electronic circuits to safeguard them from environmental damage. This thin film conforms to the contours of the circuit board, providing a barrier against moisture, dust, chemicals, and temperature extremes.
- Conformal coatings are typically 25-75 micrometers thick, about the width of a human hair.
- These coatings can be made from various materials, including acrylics, silicones, polyurethanes, and epoxies.
- The primary purpose is to protect electronic components from corrosion and electrical failures.
- Conformal coatings are transparent, allowing for visual inspection of the components underneath.
- They are often applied using methods like brushing, spraying, dipping, or automated selective coating.
Types of Conformal Coatings
Different types of conformal coatings offer unique benefits and are chosen based on the specific needs of the electronic device.
- Acrylic coatings are popular due to their ease of application and removal.
- Silicone coatings provide excellent moisture and temperature resistance, making them ideal for harsh environments.
- Polyurethane coatings offer strong chemical resistance, suitable for industrial applications.
- Epoxy coatings are known for their hardness and durability but can be challenging to remove.
- Parylene coatings are applied through a vapor deposition process, offering uniform coverage and high dielectric strength.
Applications of Conformal Coatings
Conformal coatings are used in various industries to protect electronic devices and ensure their longevity and reliability.
- Aerospace and aviation industries use conformal coatings to protect avionics from extreme temperatures and humidity.
- Automotive electronics benefit from conformal coatings to withstand vibration, temperature fluctuations, and exposure to chemicals.
- Medical devices, such as pacemakers and hearing aids, use conformal coatings to ensure reliability and safety.
- Consumer electronics, including smartphones and tablets, use these coatings to protect against moisture and dust.
- Military and defense applications rely on conformal coatings for rugged and reliable performance in harsh conditions.
Benefits of Conformal Coatings
The advantages of using conformal coatings extend beyond just protection, offering several key benefits to electronic devices.
- They enhance the reliability and lifespan of electronic components.
- Conformal coatings reduce the risk of short circuits and electrical failures.
- They provide a barrier against environmental contaminants like dust, moisture, and chemicals.
- These coatings improve the performance of electronic devices in extreme conditions.
- They can also help in reducing the weight and size of electronic assemblies by eliminating the need for bulky protective enclosures.
Challenges and Considerations
While conformal coatings offer numerous benefits, there are also challenges and considerations to keep in mind.
- Proper application is crucial to ensure effective protection; uneven coating can lead to vulnerabilities.
- Removing conformal coatings for repair or rework can be difficult, especially with materials like epoxy.
- The selection of the appropriate coating material depends on the specific environmental conditions and requirements of the application.
- Some conformal coatings may require specialized equipment for application, adding to the cost.
- Ensuring compatibility with other materials and components in the electronic assembly is essential to avoid adverse reactions.
Testing and Quality Control
To ensure the effectiveness of conformal coatings, rigorous testing and quality control measures are implemented.
- Coating thickness is measured using techniques like micrometers or non-contact methods like eddy current testing.
- Adhesion tests, such as the tape test, are conducted to ensure the coating adheres properly to the substrate.
- Environmental testing, including temperature cycling and humidity exposure, evaluates the coating's performance under extreme conditions.
- Electrical testing checks for insulation resistance and dielectric strength to ensure the coating does not interfere with the circuit's functionality.
- Visual inspection, often under UV light, helps identify any defects or areas with insufficient coverage.
Future Trends in Conformal Coatings
The field of conformal coatings is continually evolving, with new materials and technologies emerging to meet the demands of modern electronics.
- Nanocoatings are being developed to provide even thinner and more effective protection.
- Environmentally friendly coatings are gaining popularity, reducing the use of hazardous chemicals.
- Smart coatings with self-healing properties are being researched to extend the lifespan of electronic devices.
- Advances in application methods, such as robotic spraying and selective coating, improve precision and efficiency.
- Integration of conformal coatings with other protective measures, like encapsulation, offers enhanced protection for critical applications.
The Final Word on Conformal Coating
Conformal coatings are essential for protecting electronic circuits from harsh environments. They offer benefits like moisture resistance, chemical protection, and improved reliability. Different types of coatings, such as acrylic, silicone, and epoxy, cater to various needs based on their unique properties. Application methods like brushing, spraying, and dipping ensure versatility in usage.
Understanding the importance of these coatings can help in making informed decisions for electronics protection. Whether you're dealing with consumer electronics, automotive systems, or aerospace technology, choosing the right conformal coating can significantly extend the lifespan and performance of your devices.
Keep these facts in mind when considering conformal coatings for your next project. They might just be the unsung heroes that keep your electronics running smoothly in challenging conditions.
Was this page helpful?
Our commitment to delivering trustworthy and engaging content is at the heart of what we do. Each fact on our site is contributed by real users like you, bringing a wealth of diverse insights and information. To ensure the highest standards of accuracy and reliability, our dedicated editors meticulously review each submission. This process guarantees that the facts we share are not only fascinating but also credible. Trust in our commitment to quality and authenticity as you explore and learn with us.