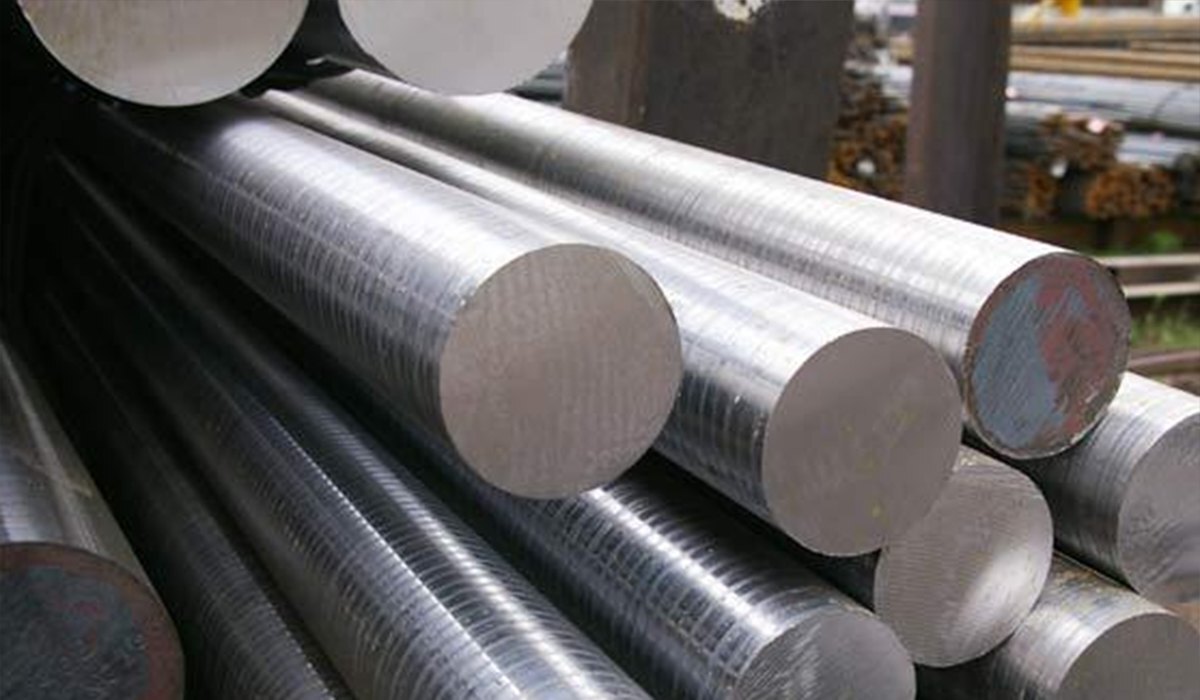
What makes Alloy 230 so special? This high-performance material stands out due to its exceptional resistance to oxidation and nitriding at high temperatures. Alloy 230 is a nickel-chromium-tungsten-molybdenum alloy, which means it can handle extreme heat without losing strength. It's commonly used in gas turbines, industrial furnaces, and chemical processing equipment. Engineers love it because it maintains its integrity even when exposed to harsh environments. Its versatility and durability make it a go-to choice for many industries. Want to know more? Let's dive into 30 fascinating facts about this incredible alloy!
Key Takeaways:
- Alloy 230, also known as Haynes 230, is a super strong and heat-resistant metal used in things like gas turbines and nuclear reactors. It's great because it lasts a really long time and can handle tough conditions.
- Alloy 230 is like a superhero metal that can withstand super high temperatures and resist corrosion. It's used in all sorts of important things, from industrial furnaces to chemical processing equipment, keeping everything running smoothly and safely.
What is Alloy 230?
Alloy 230, also known as Haynes 230, is a nickel-chromium-tungsten-molybdenum alloy. It's known for its excellent high-temperature strength and oxidation resistance. This makes it a popular choice in various industries.
-
High-Temperature Strength: Alloy 230 maintains its strength even at temperatures up to 2100°F (1149°C). This makes it ideal for applications in gas turbines and industrial furnaces.
-
Oxidation Resistance: This alloy forms a protective oxide layer, which helps it resist oxidation at high temperatures. This property extends the lifespan of components made from Alloy 230.
-
Corrosion Resistance: It offers good resistance to corrosion in both oxidizing and reducing environments. This makes it suitable for chemical processing equipment.
-
Weldability: Alloy 230 can be welded using common welding techniques. This makes it easier to fabricate complex components.
-
Ductility: Despite its strength, Alloy 230 remains ductile. This allows it to be formed into various shapes without cracking.
Applications of Alloy 230
Alloy 230's unique properties make it suitable for a wide range of applications. Here are some of the most common uses.
-
Gas Turbines: Its high-temperature strength and oxidation resistance make it ideal for turbine blades and other components.
-
Industrial Furnaces: Alloy 230 is used in furnace components due to its ability to withstand extreme temperatures.
-
Chemical Processing: Its corrosion resistance makes it suitable for equipment used in chemical processing plants.
-
Nuclear Reactors: The alloy's stability at high temperatures makes it a good choice for nuclear reactor components.
-
Heat Exchangers: Alloy 230 is used in heat exchangers due to its excellent thermal stability.
Chemical Composition of Alloy 230
Understanding the chemical makeup of Alloy 230 helps explain its remarkable properties. Here’s a breakdown of its composition.
-
Nickel (Ni): Comprises 57-63% of the alloy. Nickel provides high-temperature strength and corrosion resistance.
-
Chromium (Cr): Makes up 20-24%. Chromium enhances oxidation resistance.
-
Tungsten (W): Present at 14%. Tungsten contributes to the alloy's high-temperature strength.
-
Molybdenum (Mo): Contains 1-3%. Molybdenum improves corrosion resistance.
-
Iron (Fe): Limited to 3% max. Iron is kept low to maintain the alloy's high-temperature properties.
Mechanical Properties of Alloy 230
The mechanical properties of Alloy 230 make it a versatile material for various demanding applications.
-
Tensile Strength: It has a tensile strength of 120 ksi (827 MPa) at room temperature. This indicates its ability to withstand high stress.
-
Yield Strength: The yield strength is 55 ksi (379 MPa). This measures the stress at which the alloy begins to deform plastically.
-
Elongation: Alloy 230 has an elongation of 45% in 2 inches. This shows its ductility and ability to stretch without breaking.
-
Hardness: It has a hardness of 220 HB (Brinell Hardness). This indicates its resistance to deformation and wear.
-
Creep Resistance: The alloy exhibits excellent creep resistance, meaning it can withstand long-term exposure to high stress and temperature without deforming.
Fabrication and Machining of Alloy 230
Fabricating and machining Alloy 230 requires specific techniques due to its unique properties.
-
Cold Working: Alloy 230 can be cold worked to improve its strength and hardness. This involves deforming the alloy at room temperature.
-
Hot Working: It can also be hot worked at temperatures between 1600°F and 2250°F (870°C to 1230°C). This makes it easier to shape and form.
-
Machining: Machining Alloy 230 requires carbide tools and low cutting speeds. This helps prevent tool wear and maintain precision.
-
Heat Treatment: The alloy can be heat treated to enhance its mechanical properties. This involves heating it to a specific temperature and then cooling it rapidly.
-
Annealing: Annealing Alloy 230 at 2100°F (1149°C) helps relieve internal stresses and improve ductility.
Advantages of Using Alloy 230
Alloy 230 offers several advantages that make it a preferred choice in many industries.
-
Longevity: Components made from Alloy 230 have a longer lifespan due to their resistance to high temperatures and corrosion.
-
Versatility: Its ability to withstand various environmental conditions makes it suitable for a wide range of applications.
-
Reliability: The alloy's consistent performance under extreme conditions ensures reliability in critical applications.
-
Cost-Effectiveness: Despite its higher initial cost, the durability and low maintenance requirements of Alloy 230 make it cost-effective in the long run.
-
Safety: Using Alloy 230 in high-temperature and corrosive environments enhances safety by reducing the risk of component failure.
The Final Word on Alloy 230
Alloy 230 stands out for its high-temperature strength, oxidation resistance, and versatility. Used in industries like aerospace, chemical processing, and power generation, it handles extreme conditions with ease. Its unique composition, featuring nickel, chromium, and tungsten, gives it durability and reliability.
From jet engines to nuclear reactors, Alloy 230 proves its worth. Its ability to maintain integrity under stress makes it indispensable. Whether you're an engineer, scientist, or just curious, understanding this alloy's properties can be a game-changer.
Remember, the right material can make all the difference in demanding applications. Alloy 230 isn't just a metal; it's a solution to many industrial challenges. Keep these facts in mind next time you encounter high-stress environments. This alloy's capabilities are truly remarkable.
Frequently Asked Questions
Was this page helpful?
Our commitment to delivering trustworthy and engaging content is at the heart of what we do. Each fact on our site is contributed by real users like you, bringing a wealth of diverse insights and information. To ensure the highest standards of accuracy and reliability, our dedicated editors meticulously review each submission. This process guarantees that the facts we share are not only fascinating but also credible. Trust in our commitment to quality and authenticity as you explore and learn with us.